Last updated on
Discover the world of sustainable alternatives to cement as we delve into innovative and eco-friendly solutions for a greener construction industry.
Welcome to my latest blog post where we will be exploring sustainable alternatives to cement. Cement is a common building material that has been used for centuries, but its production and use have a significant impact on the environment.
From carbon emissions during production to the destruction of natural habitats, it’s time we start looking for more eco-friendly options. In this article, I’ll be sharing some exciting alternatives that are not only better for the environment but also cost-effective.
So if you’re interested in creating beautiful structures without harming the planet or breaking your bank account, keep reading!
Why Are Alternatives to Cement Important
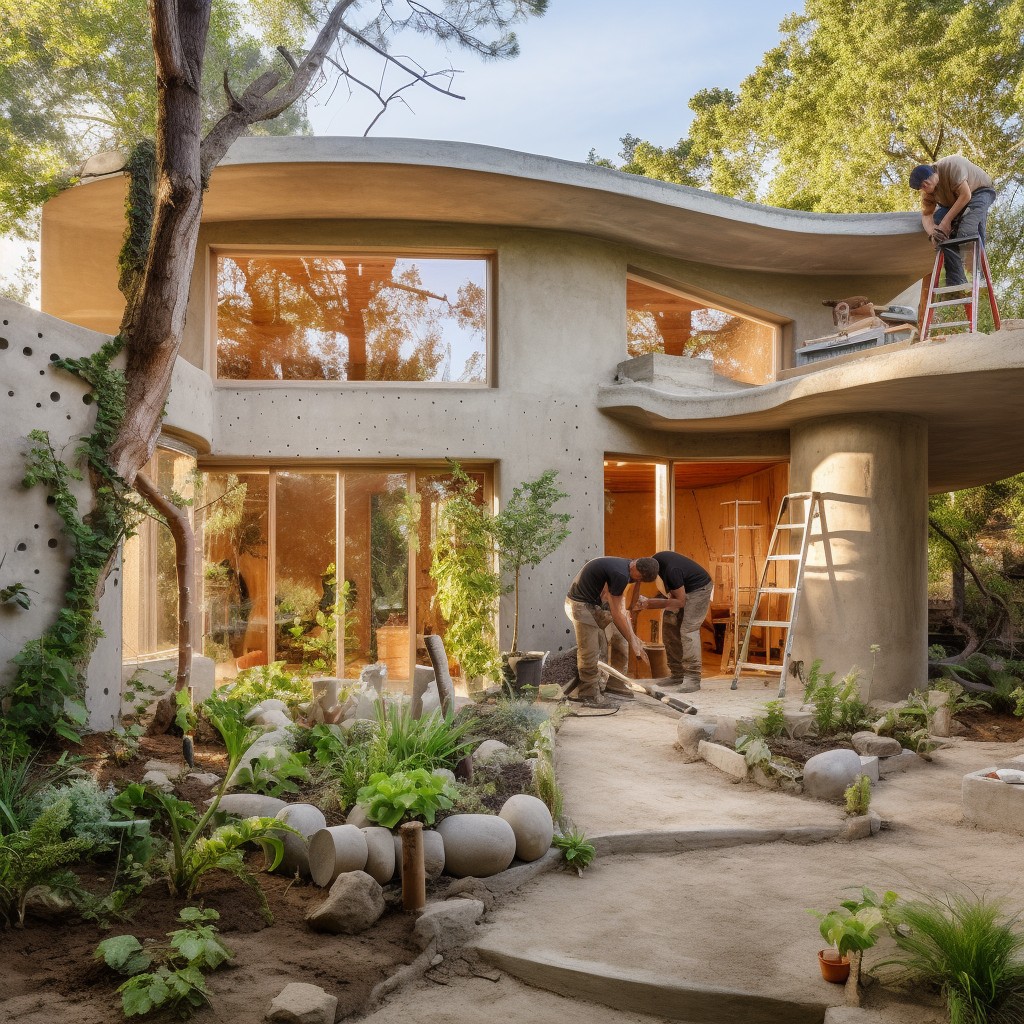
Cement manufacturing is responsible for approximately 8% of global carbon dioxide emissions, making it one of the largest contributors to greenhouse gas emissions. Cement production requires large amounts of energy and water resources while also contributing to deforestation due to mining activities.
The good news is that there are sustainable alternatives available that can help reduce these negative impacts. By using eco-friendly construction materials like fly ash or slag cement instead of traditional Portland cement, we can significantly decrease our carbon footprint without sacrificing quality or durability.
Moreover, alternative cements often require less energy during their production process than traditional Portland cement does; this means fewer greenhouse gases emitted into the atmosphere from power plants generating electricity needed for manufacturing processes.
Dangerous for Human Health
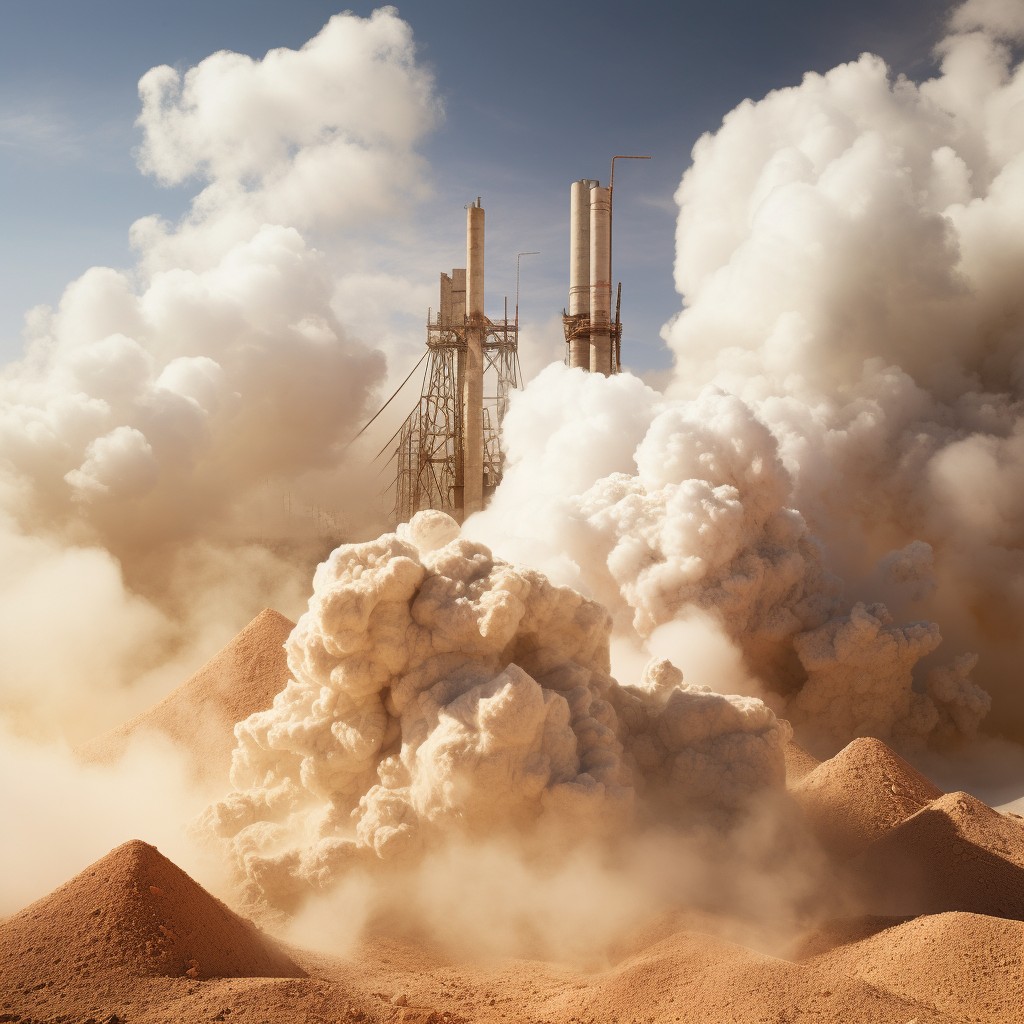
The dust generated during the manufacturing process contains harmful substances such as silica, which can cause lung cancer and other respiratory diseases. Workers in cement factories are at high risk of developing these conditions due to prolonged exposure.
The use of cement in construction also poses health risks. When mixed with water, it releases alkaline compounds that can cause skin irritation or burns if they come into contact with human skin.
It’s essential to consider these dangers when choosing building materials for your projects.
Dangerous for the Environment
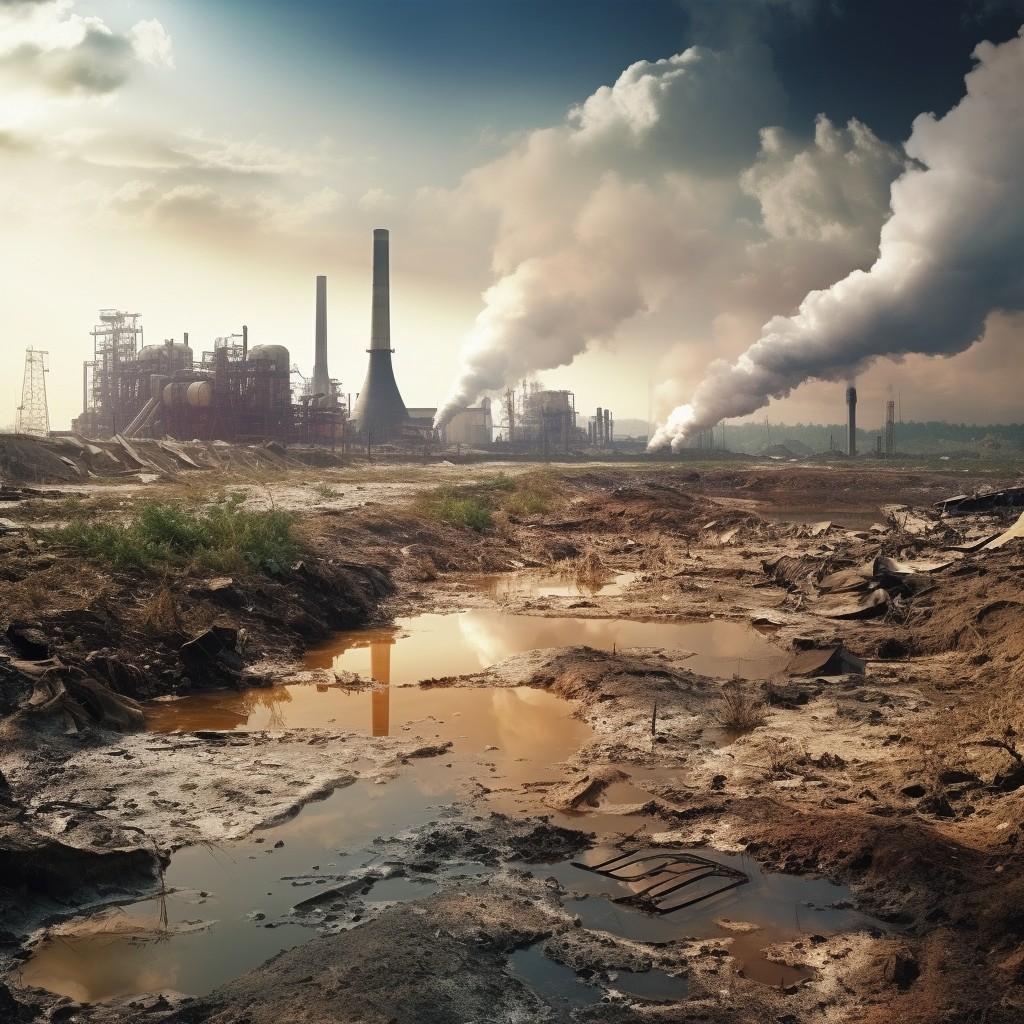
The process involves heating limestone and other materials at high temperatures, which releases large amounts of greenhouse gases into the atmosphere. Cement production requires vast amounts of water and energy resources.
The environmental impact doesn’t stop there; cement also has a significant impact on natural habitats. Quarrying for raw materials destroys ecosystems and wildlife habitats while leaving behind scars on landscapes that can take decades or even centuries to recover.
Furthermore, when concrete structures reach their end-of-life stage, they often end up in landfills where they continue to release harmful chemicals into the environment as they decompose over time.
It’s clear that we need sustainable alternatives to traditional cement if we want to reduce our negative impact on the environment.
Fly Ash As an Alternative
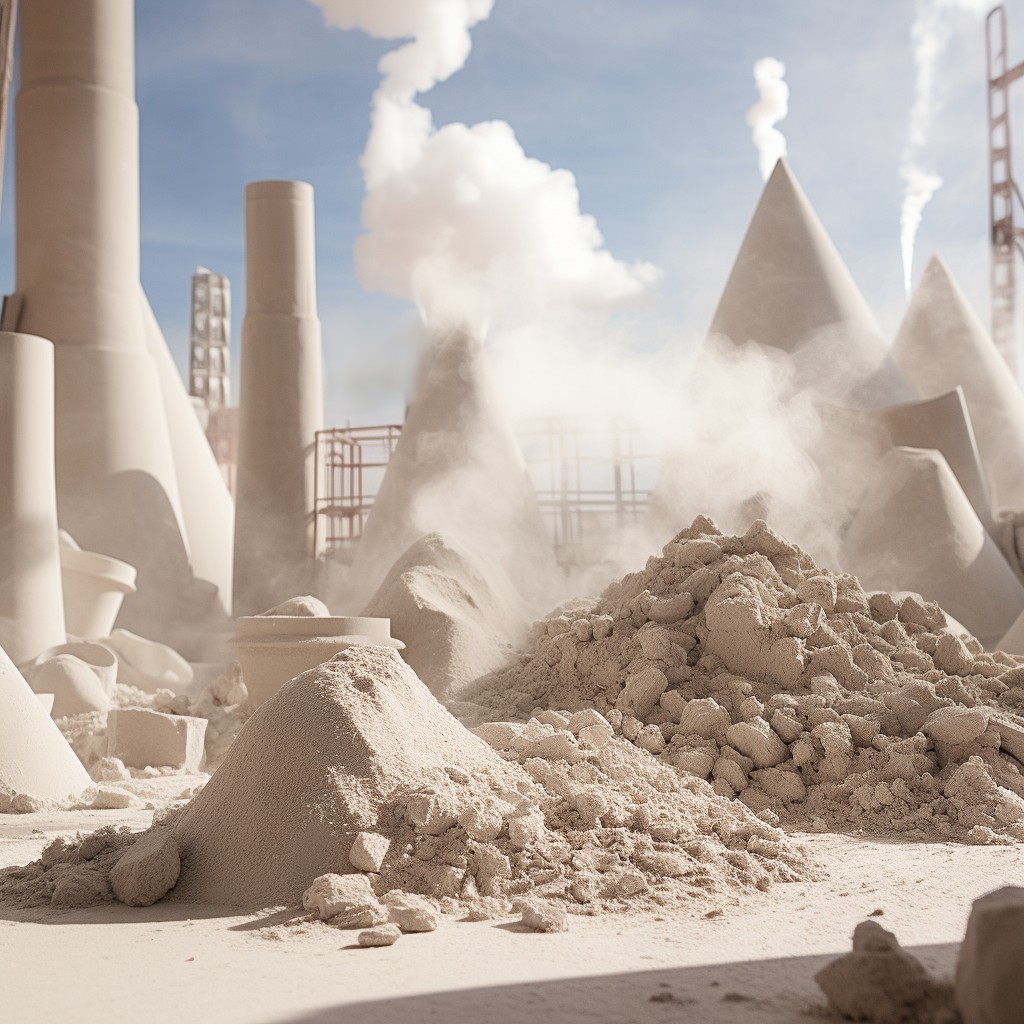
It’s a cost-effective solution that reduces the amount of waste sent to landfills while also reducing carbon emissions. Fly ash can be used in concrete, mortar, and grout mixes, making it versatile for various construction projects.
One significant advantage of using fly ash is its ability to improve the durability and strength of concrete structures. The material contains silica fume which reacts with calcium hydroxide during hydration resulting in denser concrete with fewer pores that are less susceptible to cracking or damage from freeze-thaw cycles.
Another benefit is its low permeability which makes it ideal for use in marine environments where saltwater corrosion can cause significant damage over time.
Fly ash provides an excellent sustainable alternative option without compromising on quality or performance.
Use of Slag Cement
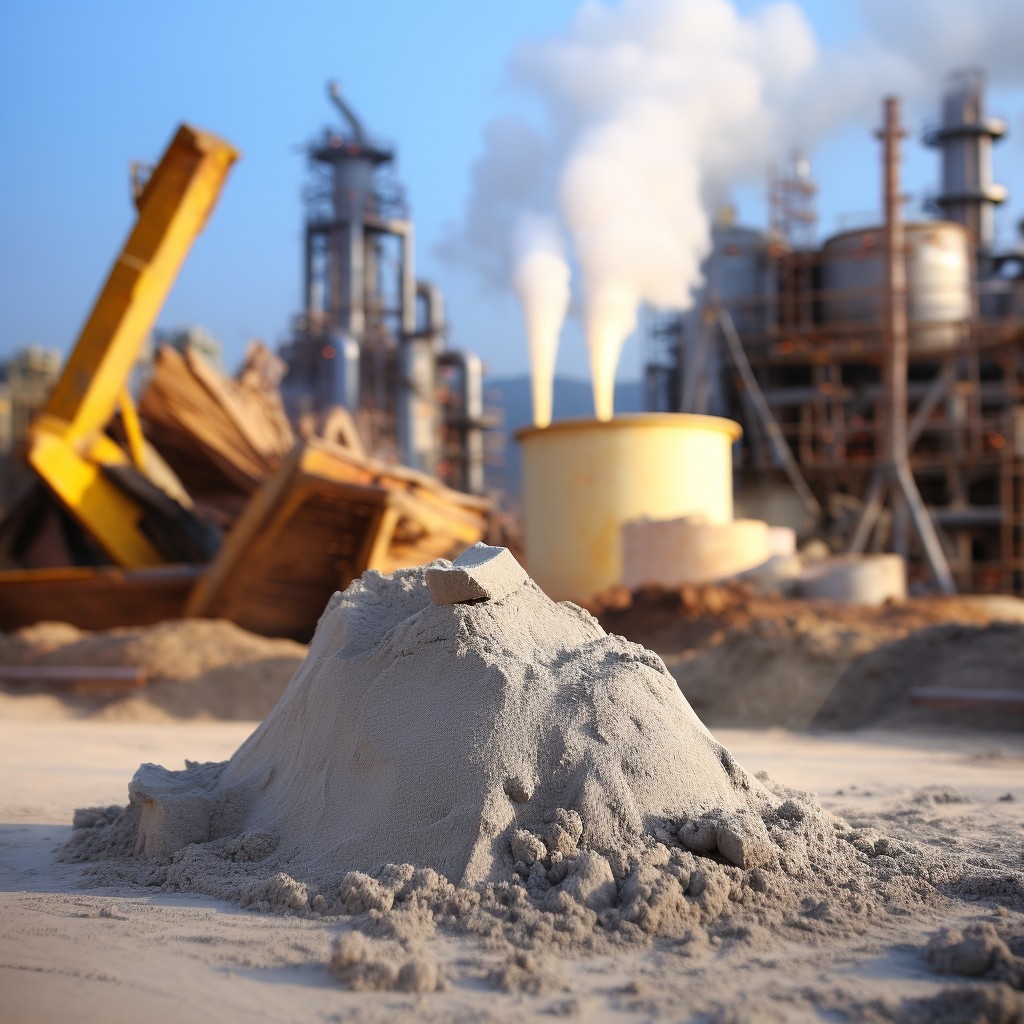
It’s made from blast furnace slag, which is a waste product that would otherwise end up in landfills. The production of slag cement emits fewer greenhouse gases than traditional Portland cement, making it an eco-friendly option.
The use of slag in construction also offers several benefits such as improved durability and reduced permeability. Slag can be used to replace up to 50% of the total volume of Portland Cement without compromising on strength or performance.
Using slag reduces energy consumption during production since it requires lower temperatures compared to regular concrete mixtures. This translates into cost savings for builders while reducing carbon emissions associated with manufacturing processes.
Silica Fume in Eco-friendly Construction
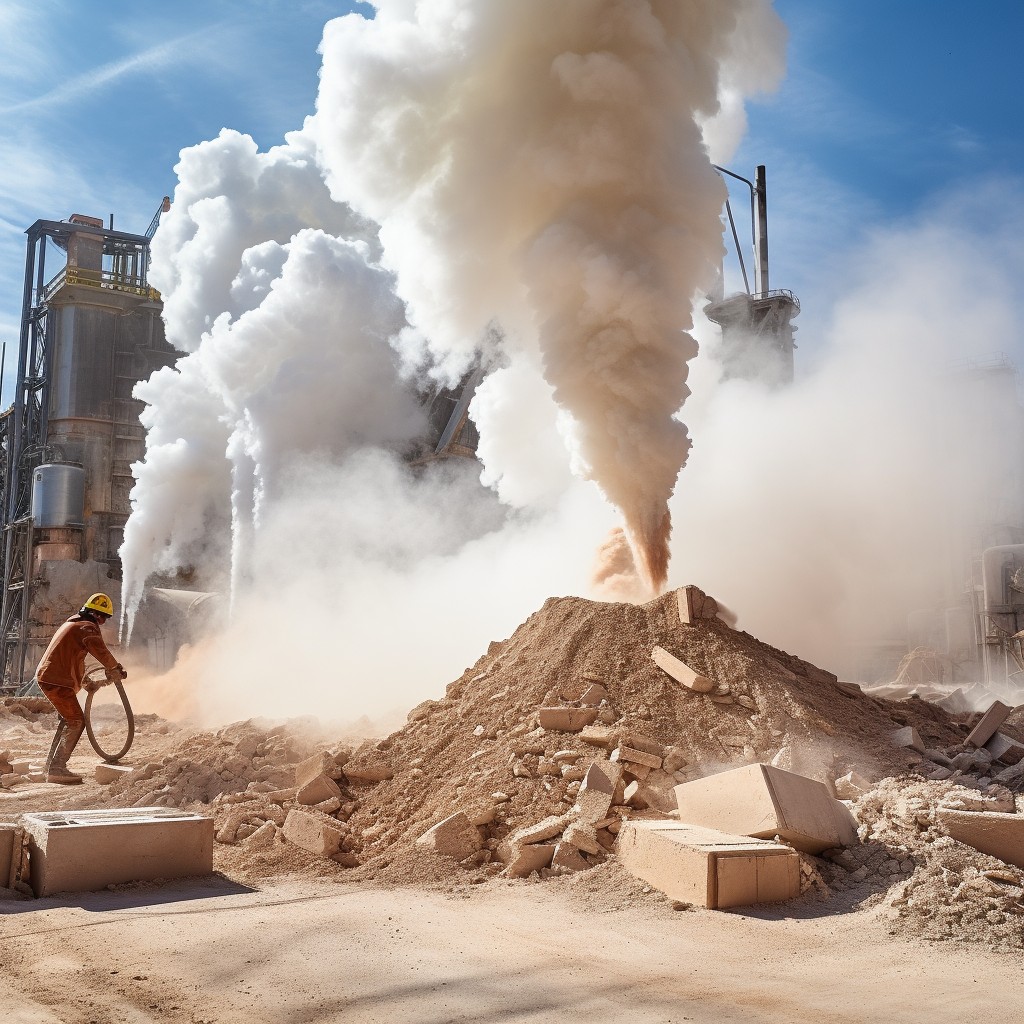
It’s an ultra-fine powder that can be used as a partial replacement for cement in concrete mixtures. Silica fume has excellent pozzolanic properties, which means it reacts with calcium hydroxide to form additional cementitious compounds.
Using silica fume in concrete mixtures reduces the amount of Portland cement required, resulting in lower carbon emissions during production. Silica fumes’ high reactivity improves the strength and durability of concrete structures while reducing permeability.
In eco-friendly construction projects where sustainability is key, using silica fumes can significantly reduce environmental impact without compromising on quality or performance.
Rice Husk Ash Cement
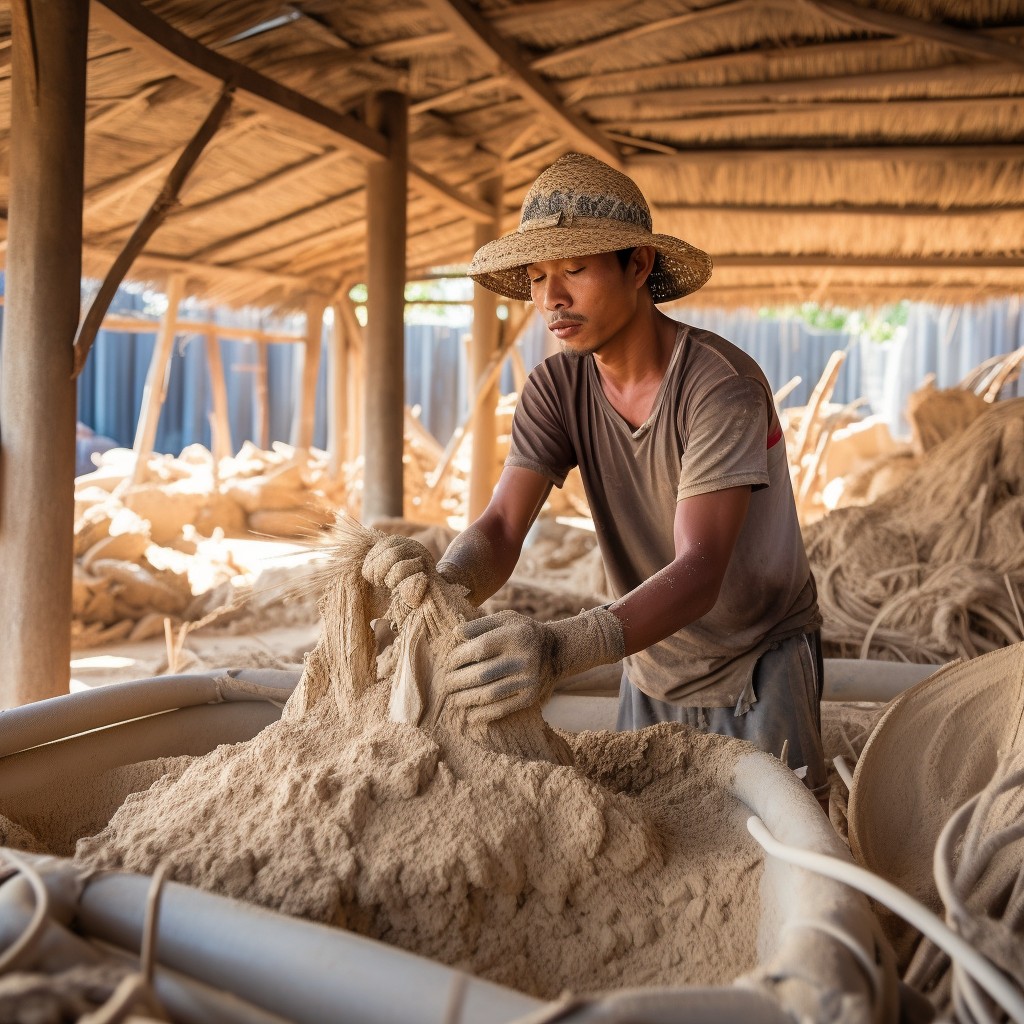
Rice husks are the outer layer of rice grains and are usually discarded as waste. However, they can be transformed into ash through controlled burning, which can then be used as a pozzolanic material in cement production.
This type of cement has several benefits over traditional Portland cement. For one, it requires less energy to produce since rice husks are readily available and do not require high-temperature kilns for processing like limestone does.
Using rice husk ash reduces carbon emissions by up to 30% compared to regular Portland cement.
Another advantage is its durability; studies have shown that structures built with this type of concrete have higher compressive strength than those made with ordinary Portland Cement (OPC). It also offers better resistance against chemical attacks such as acid rain or seawater corrosion.
Rice Husk Ash Cement provides an eco-friendly solution for construction projects while maintaining structural integrity and reducing costs associated with energy consumption during production processes.
Metakaolin Usage in Buildings
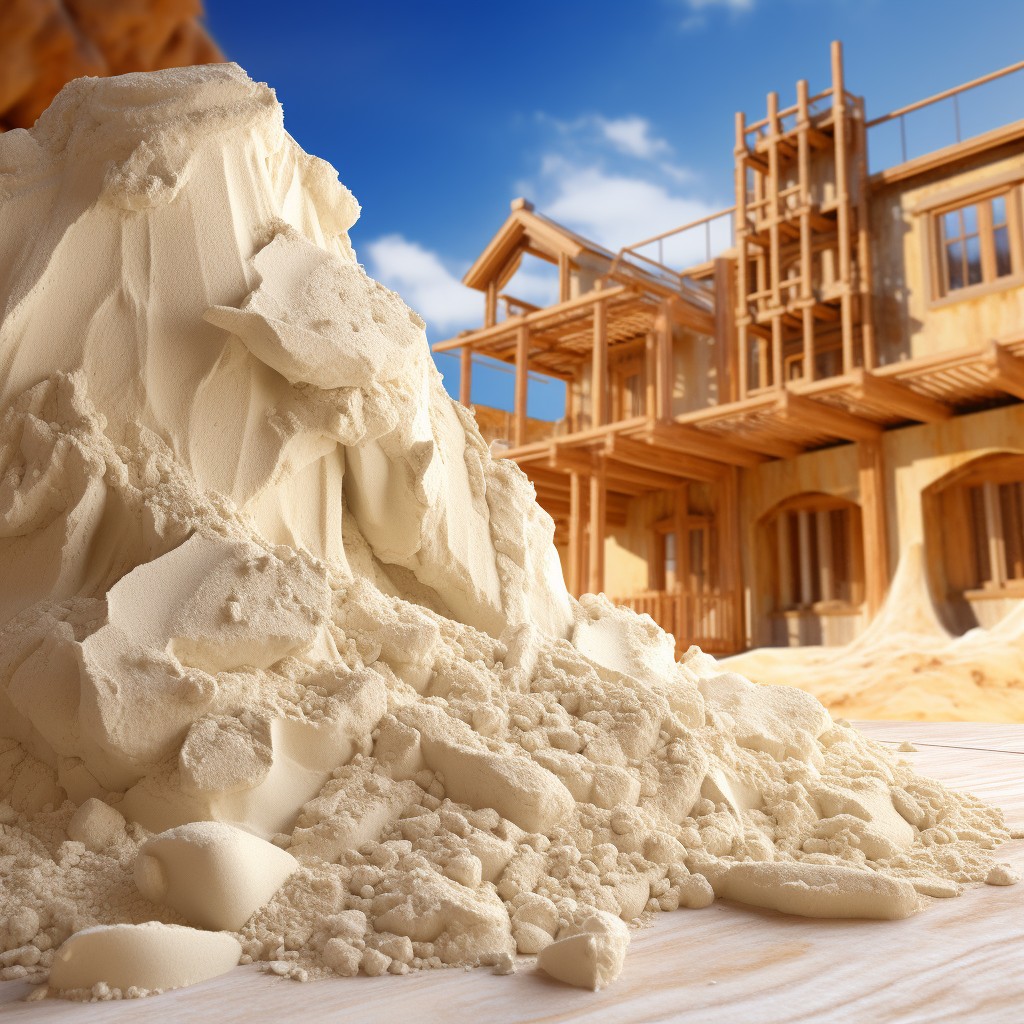
It’s made by calcining kaolin clay at high temperatures, which results in a highly reactive and amorphous substance. Metakaolin has been found to improve the strength and durability of concrete while reducing its carbon footprint.
One major advantage of metakaolin is that it requires less energy to produce than traditional cement, resulting in lower greenhouse gas emissions during production. It reduces the amount of water needed for mixing concrete without compromising its workability or setting time.
Another benefit is that metakaolin enhances the chemical resistance and durability of concrete structures due to its high reactivity with calcium hydroxide produced during hydration. This makes it ideal for use in harsh environments such as marine structures or industrial facilities where corrosion can be an issue.
Using metakaolin instead of traditional cement not only benefits our environment but also improves the quality and longevity of our buildings’ infrastructure.
Ferrock: A Novel, Iron-based Material
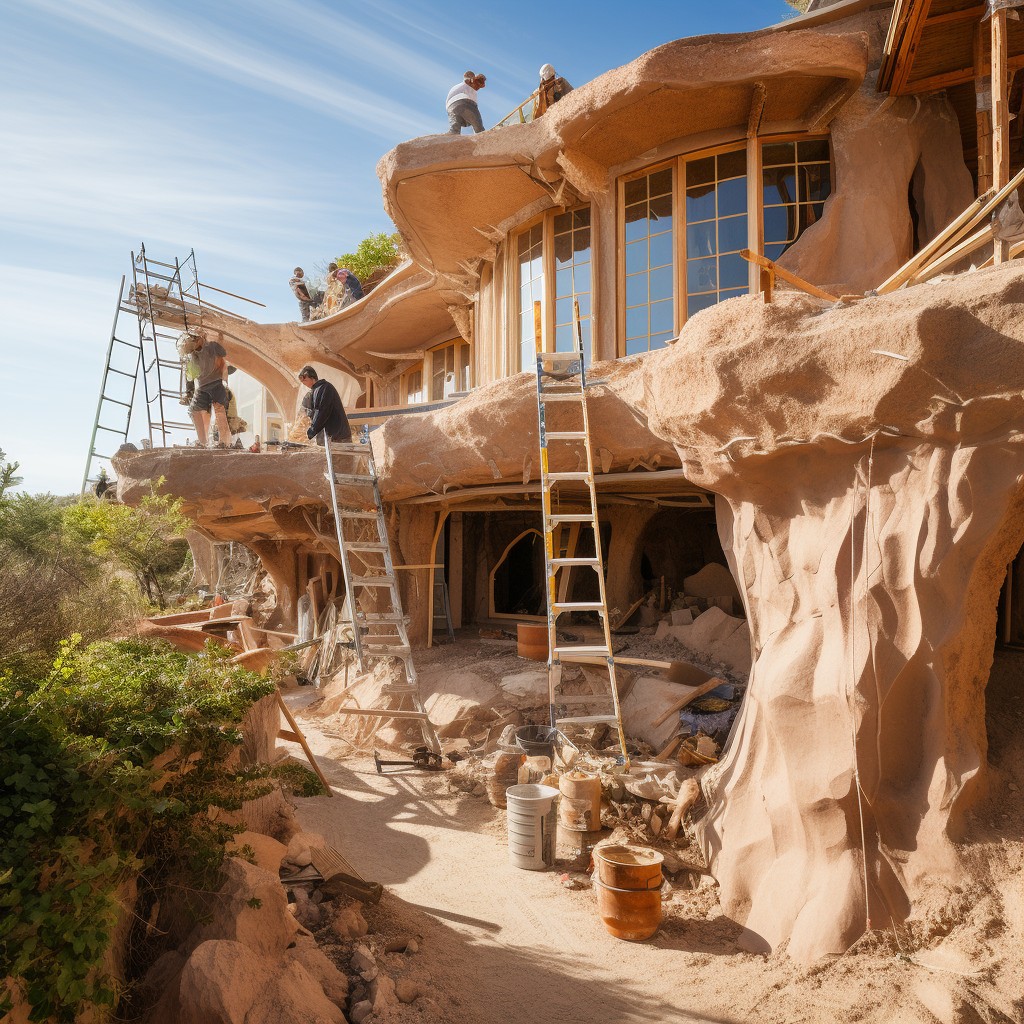
It’s made from recycled materials such as steel dust, which is combined with waste carbon dioxide to create a durable and eco-friendly alternative to cement. This iron-based material not only reduces the amount of waste going into landfills but also absorbs carbon dioxide during its production process.
One of the most significant advantages of Ferrock over traditional cement is its strength. It can withstand high levels of pressure without cracking or breaking, making it ideal for use in construction projects that require durability.
Another benefit of Ferrock is its ability to self-heal when exposed to moisture or air. The iron particles within the material react with these elements, creating more binding agents that strengthen the structure further.
Moreover, this novel building material has excellent insulation properties due to its low thermal conductivity; thus reducing energy consumption by maintaining indoor temperatures at comfortable levels throughout all seasons.
Hempcrete: Sustainable Building Material
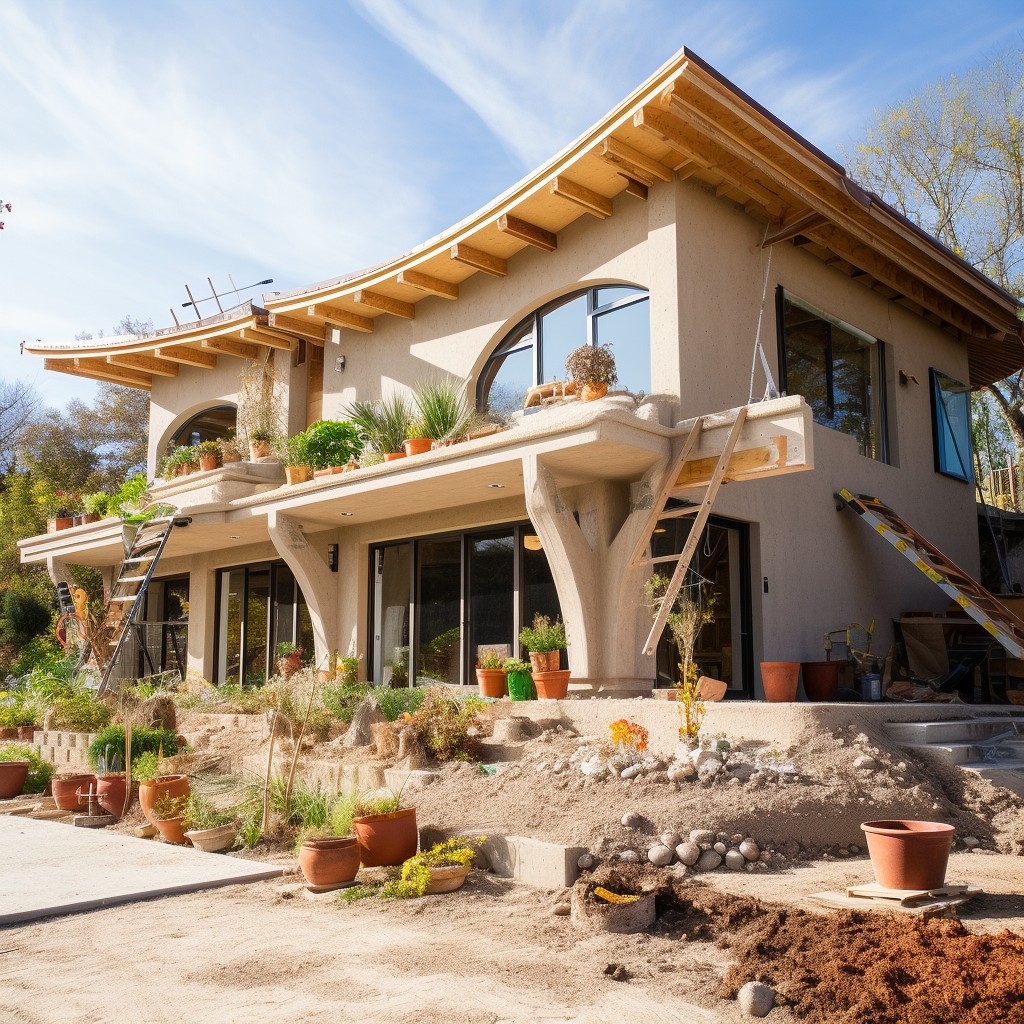
It’s made from the woody core of hemp plants mixed with lime and water, creating a lightweight yet durable material that can be used for walls, floors, and roofs. Hempcrete is not only eco-friendly but also provides excellent insulation properties.
One of the significant advantages of using hempcrete as an alternative to cement is its carbon-negative nature. The production process absorbs more CO2 than it emits, making it an ideal choice for those looking to reduce their carbon footprint.
Another benefit of using hempcrete in construction projects is its breathability. Unlike traditional concrete structures that trap moisture inside walls leading to mold growth or rotting wood frames over time due to trapped moisture; Hempcrete allows air circulation through the structure preventing such issues from occurring.
Moreover, this natural building material requires minimal energy consumption during production compared with conventional cement-based materials which require high temperatures during manufacturing processes resulting in higher greenhouse gas emissions.
Geopolymer Cement for Reduced CO2 Emissions
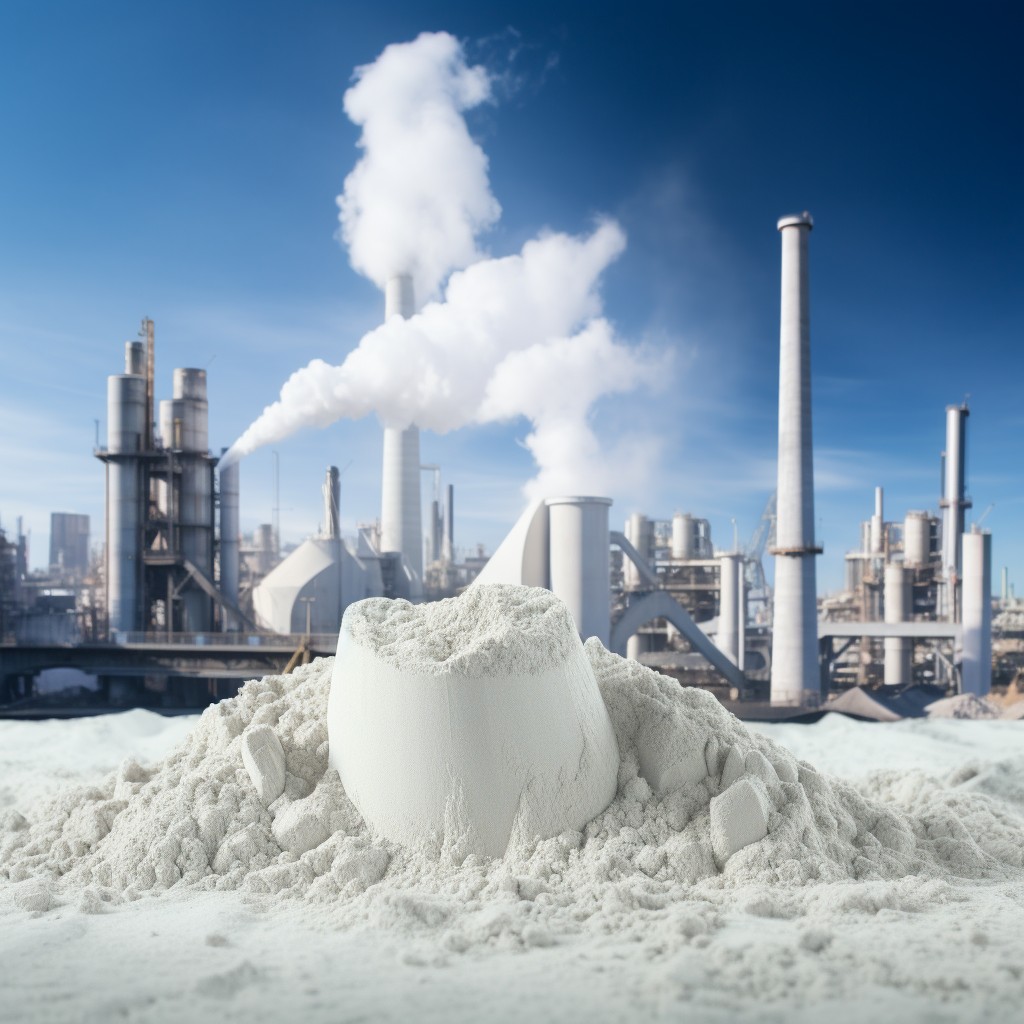
It is made by mixing industrial waste materials such as fly ash, slag, and silica fume with an alkaline solution to create a binder that can be used in construction. This process produces significantly less carbon dioxide emissions compared to traditional Portland cement production.
In addition to its environmental benefits, geopolymer cement also has superior strength and durability properties compared to conventional concrete. It can withstand high temperatures and harsh chemicals without deteriorating or losing its structural integrity.
One of the most significant advantages of geopolymer cements is their ability to use waste materials as raw ingredients instead of mining for new resources like limestone for traditional Portland Cement production. This reduces the amount of energy required during manufacturing while simultaneously reducing landfill space requirements.
Mycelium-Based Bio-cement
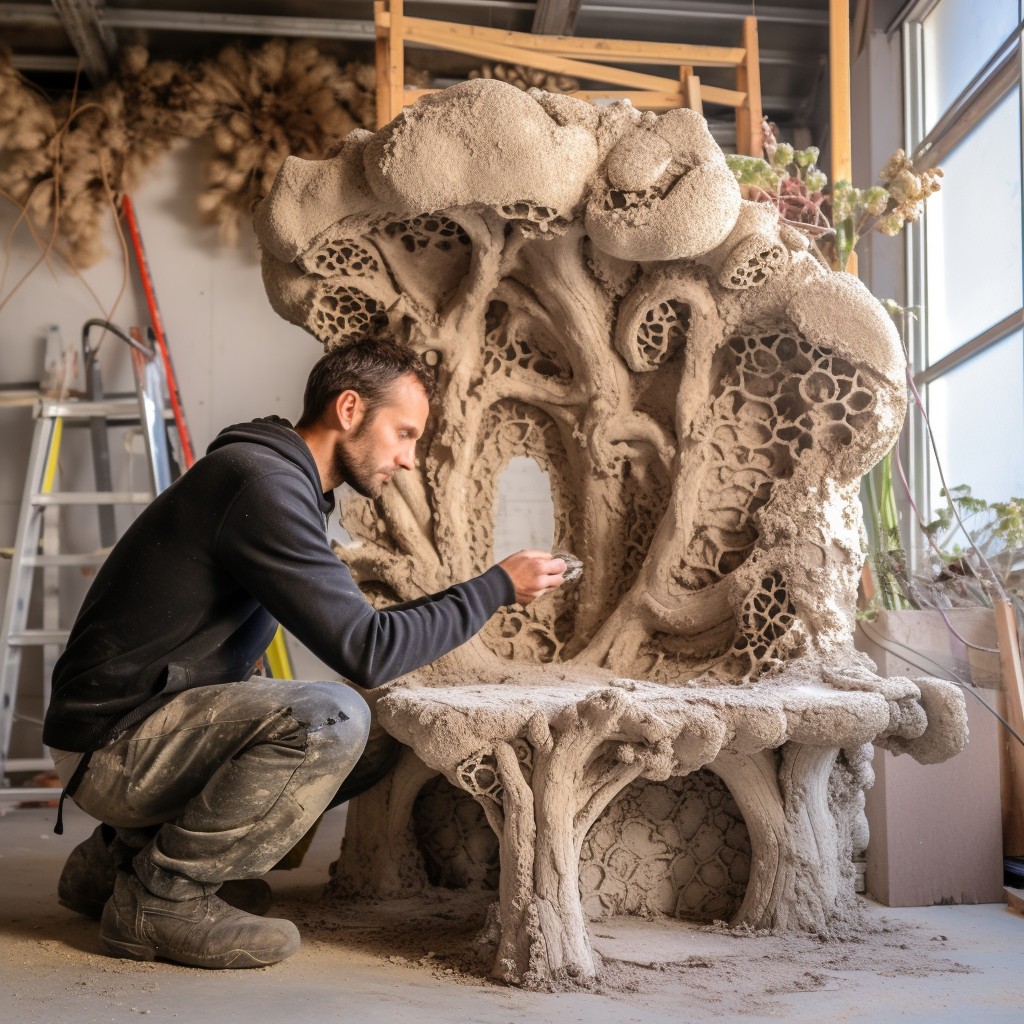
It’s made from the roots of mushrooms, which are called mycelia. These mycelia can grow into a strong and durable material that can be used for construction purposes.
The process of creating Mycelium-Based Bio-cement involves growing the mycelia in a controlled environment with organic waste materials such as sawdust or agricultural waste products like corn stalks. The resulting product is then dried out to create an incredibly strong building material.
One significant advantage of using Mycelium-Based Bio-cement is its sustainability factor; it’s biodegradable, non-toxic, and requires less energy during production than traditional cement. It has excellent insulation properties making it ideal for use in walls or roofs.
Benefits of Alkali-Activated Cements

They are made by mixing an alkaline activator, such as sodium hydroxide or potassium hydroxide, with a source of alumina and silica. This results in the formation of calcium silicate hydrate (C-S-H) gel that binds the mixture together.
One significant benefit of alkali-activated cements is their lower carbon footprint compared to traditional cement production. The manufacturing process for these types of cements produces up to 80% less CO2 emissions than Portland cement production.
Another advantage is their durability and resistance to corrosion, making them ideal for use in harsh environments like marine structures or chemical plants. Alkali-activated cements also have excellent fire resistance properties due to their high melting point.
Moreover, they can be produced using various waste materials such as fly ash from coal-fired power plants or blast furnace slag from steel mills instead of virgin raw materials which reduces landfill waste while providing cost savings on construction projects.
Waste Glass Powder in Construction
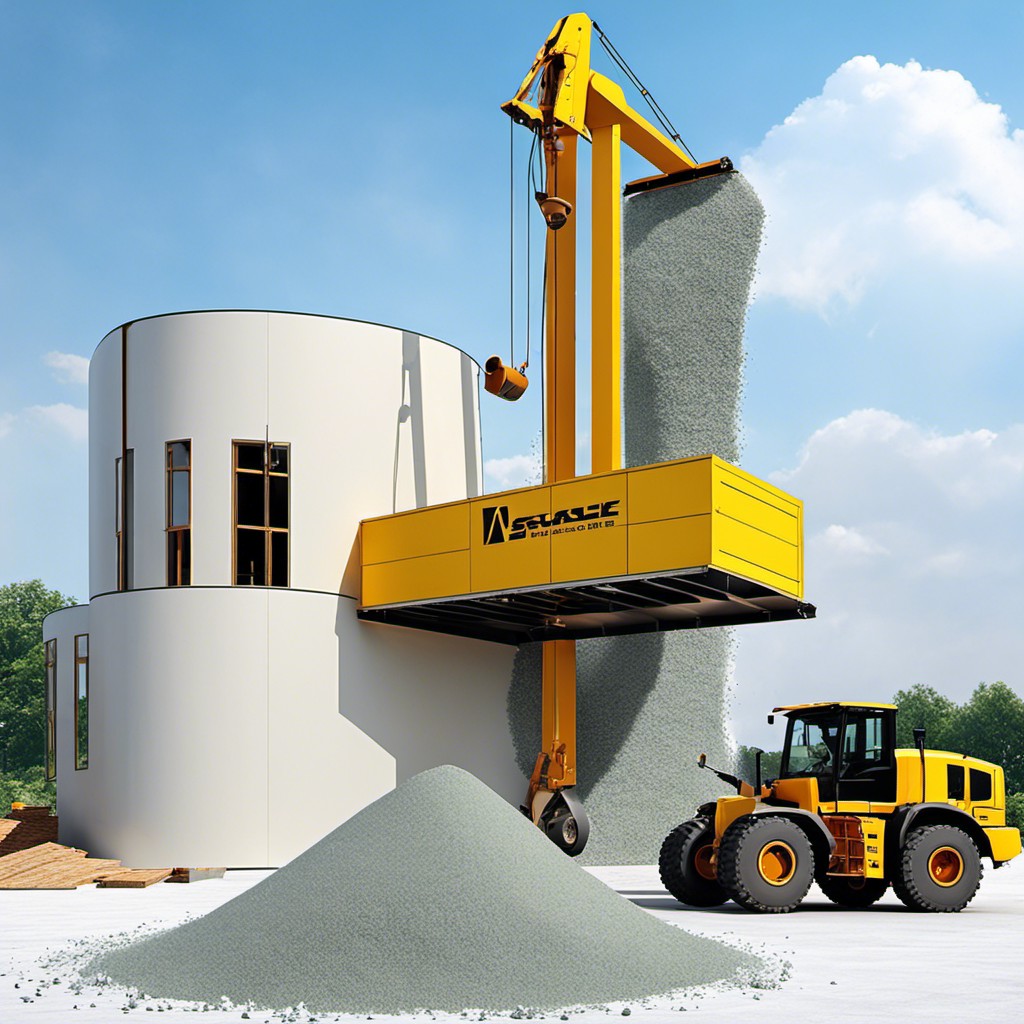
Waste glass powder (WGP) is a byproduct of recycled glass that can be used as a partial replacement for cement in concrete production. This alternative not only reduces waste but also improves the durability and strength of concrete.
The use of WGP has been found to increase compressive strength, reduce permeability, and improve resistance to chemical attacks compared to traditional cement-based mixes. Using WGP can help reduce carbon emissions associated with cement production.
Incorporating waste glass powder into construction projects not only provides an eco-friendly solution but also adds aesthetic value due to its unique appearance when mixed with concrete or other building materials.
Application of Aluminum Cement
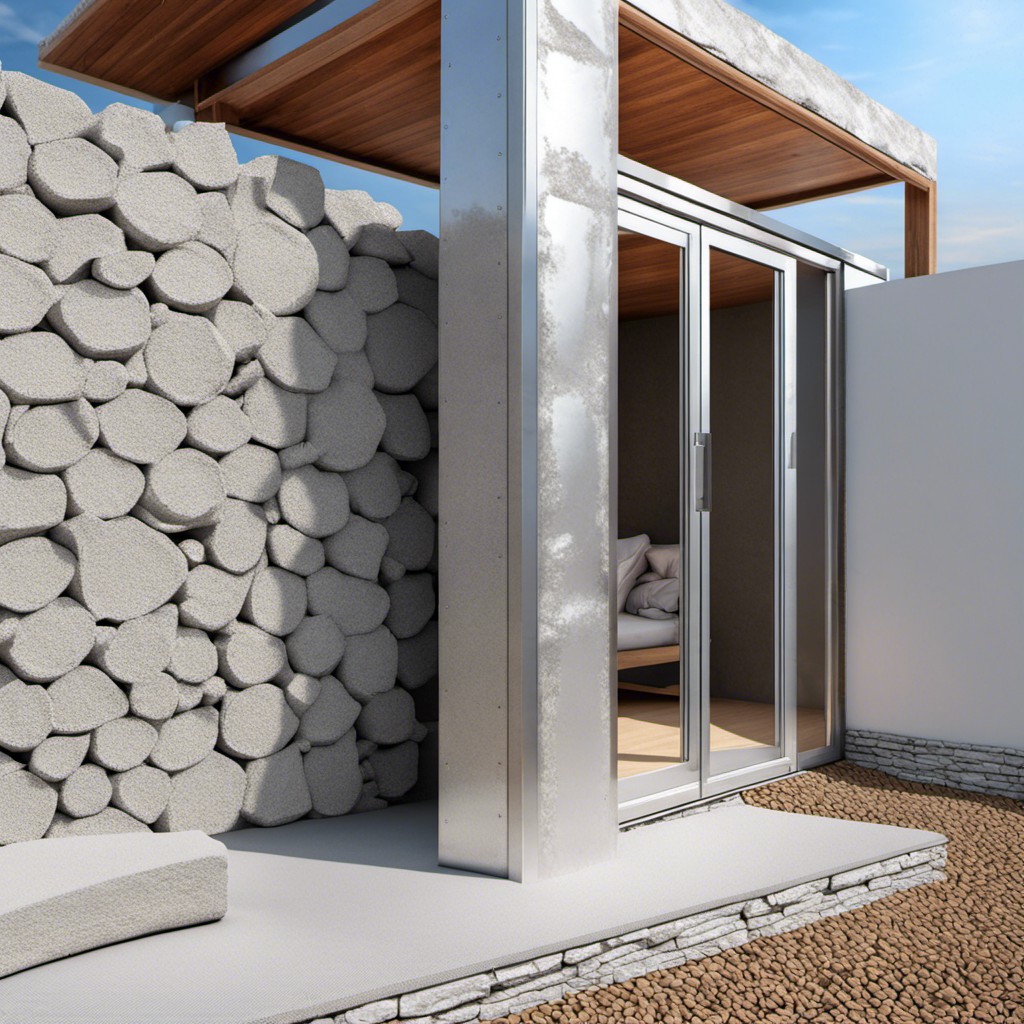
It’s made by combining aluminum powder with calcium hydroxide and water, resulting in a chemical reaction that produces hydrogen gas and heat. The mixture then hardens into a solid material similar to concrete.
One of the significant advantages of using aluminum cement is its high strength and durability, making it ideal for building structures that require resistance against harsh weather conditions or heavy loads. This type of eco-friendly construction material has excellent fire-resistant properties due to the formation of an insulating layer when exposed to high temperatures.
Another benefit is its low carbon footprint compared to conventional Portland cement production methods since it requires less energy during manufacturing processes. This makes it an attractive option for those looking for sustainable alternatives without compromising on quality or performance.
Seawater-Mixed Concrete
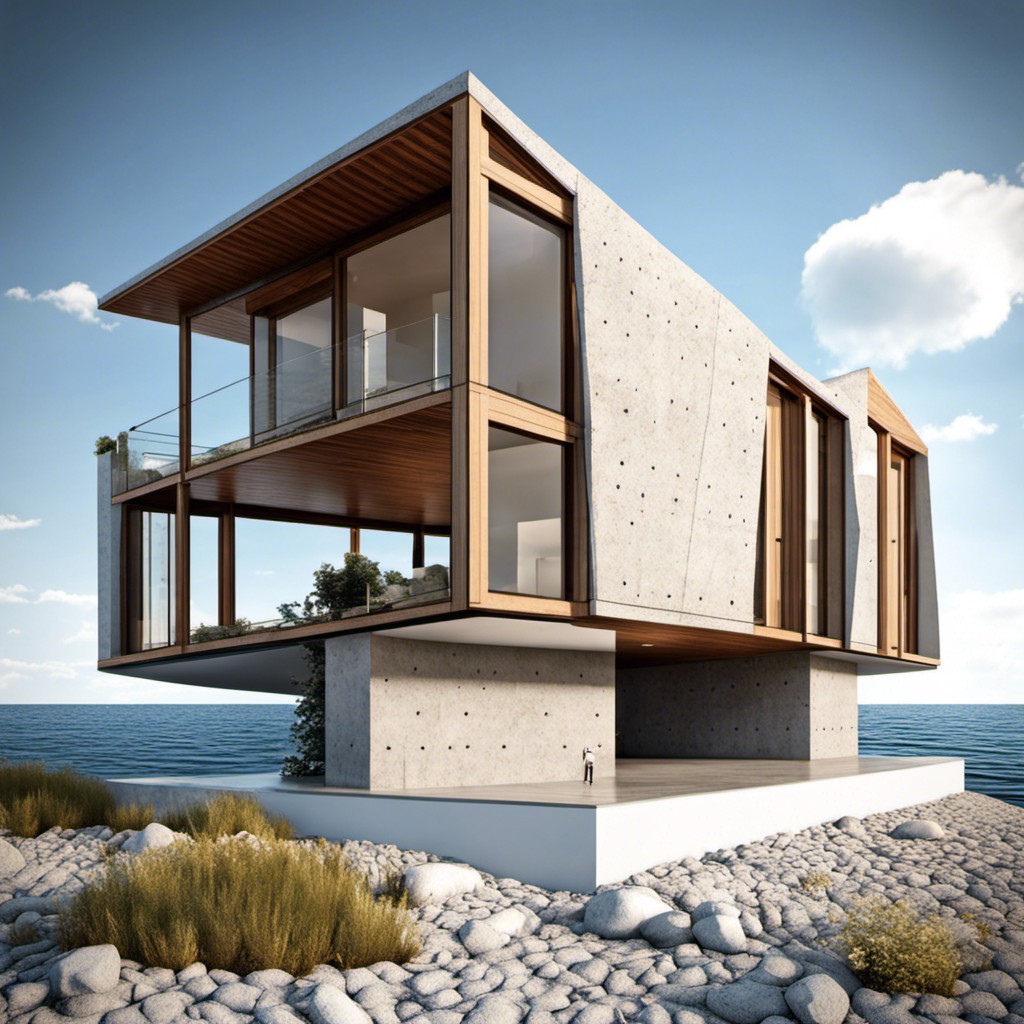
Seawater-mixed concrete has been found to have similar strength and durability as traditional concrete mixed with freshwater.
The use of seawater in construction also helps reduce the carbon footprint of cement production. The process involves using saltwater-tolerant admixtures that prevent corrosion of steel reinforcements and ensure the longevity of structures built with this type of mix.
However, it’s important to note that while seawater-mixed concrete may seem like a perfect solution, it does come with some drawbacks. The high salt content can cause corrosion over time if not adequately addressed during mixing and curing processes.
CarbonCure Technology
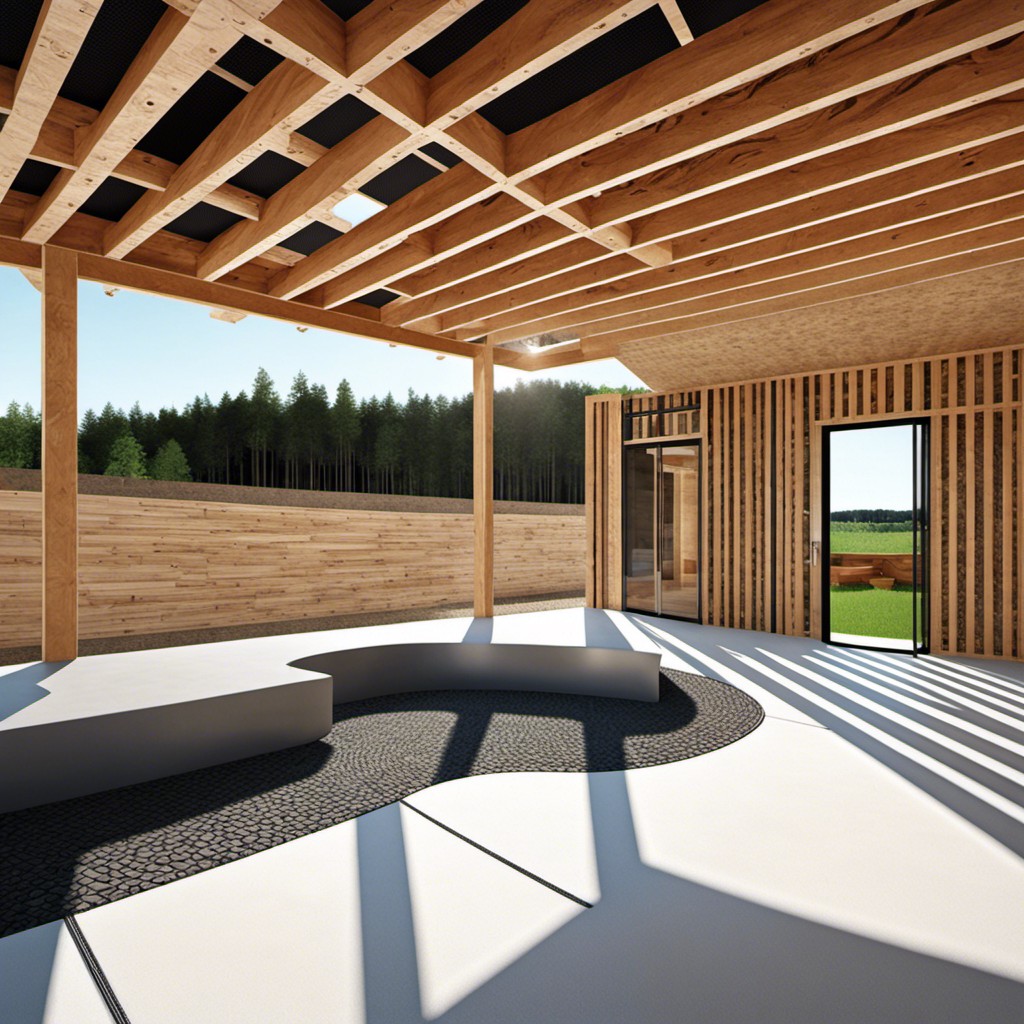
This technology involves injecting carbon dioxide (CO2) into concrete during production, which results in stronger and more durable structures. The CO2 reacts with calcium ions to form calcium carbonate, which fills up the pores of the concrete and makes it denser.
The use of CarbonCure Technology not only enhances structural integrity but also reduces carbon emissions by sequestering CO2 within the building material itself. It’s estimated that for every cubic meter of concrete produced using this technology, around 20 kilograms of CO2 can be captured permanently.
This eco-friendly solution has already been implemented in various projects worldwide, including airports, hospitals and commercial buildings.
Carbon Mineralization Techniques
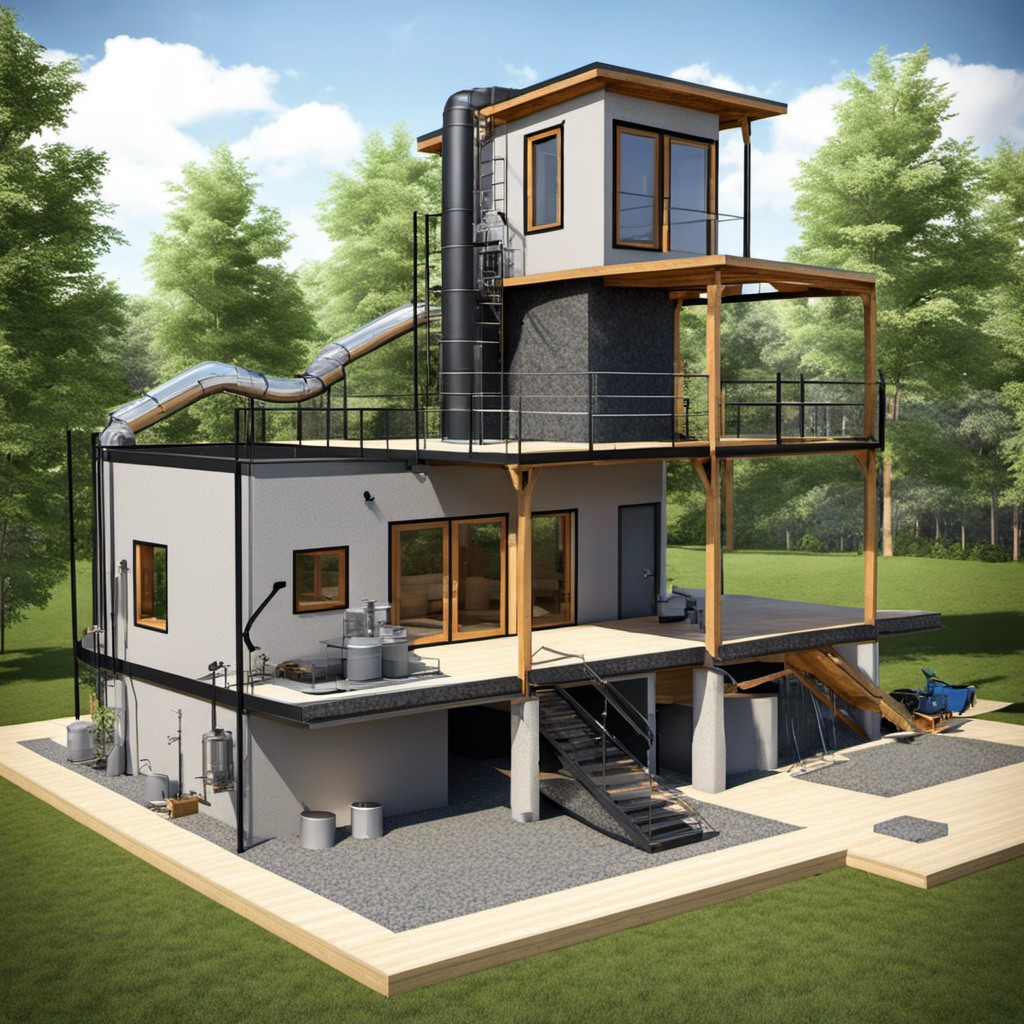
This process involves capturing carbon dioxide emissions and converting them into stable minerals that can be used in construction mterials. The captured CO2 is mixed with water and injected into porous rocks, where it reacts with the minerals to form solid carbonates.
This technique not only reduces greenhouse gas emissions but also creates a valuable building material that can replace traditional cement. Carbonated aggregates produced from this method have been shown to have similar strength properties as conventional concrete, making them an excellent substitute for environmentally harmful materials.
One of the most significant advantages of carbon mineralization techniques is their scalability potential; they could potentially capture large amounts of CO2 emitted by industrial processes such as power plants or factories while producing useful building materials simultaneously.
Using innovative technologies like carbon mineralization offers us an opportunity to reduce our environmental impact while still meeting our construction needs sustainably.
Microbial Cementation Process
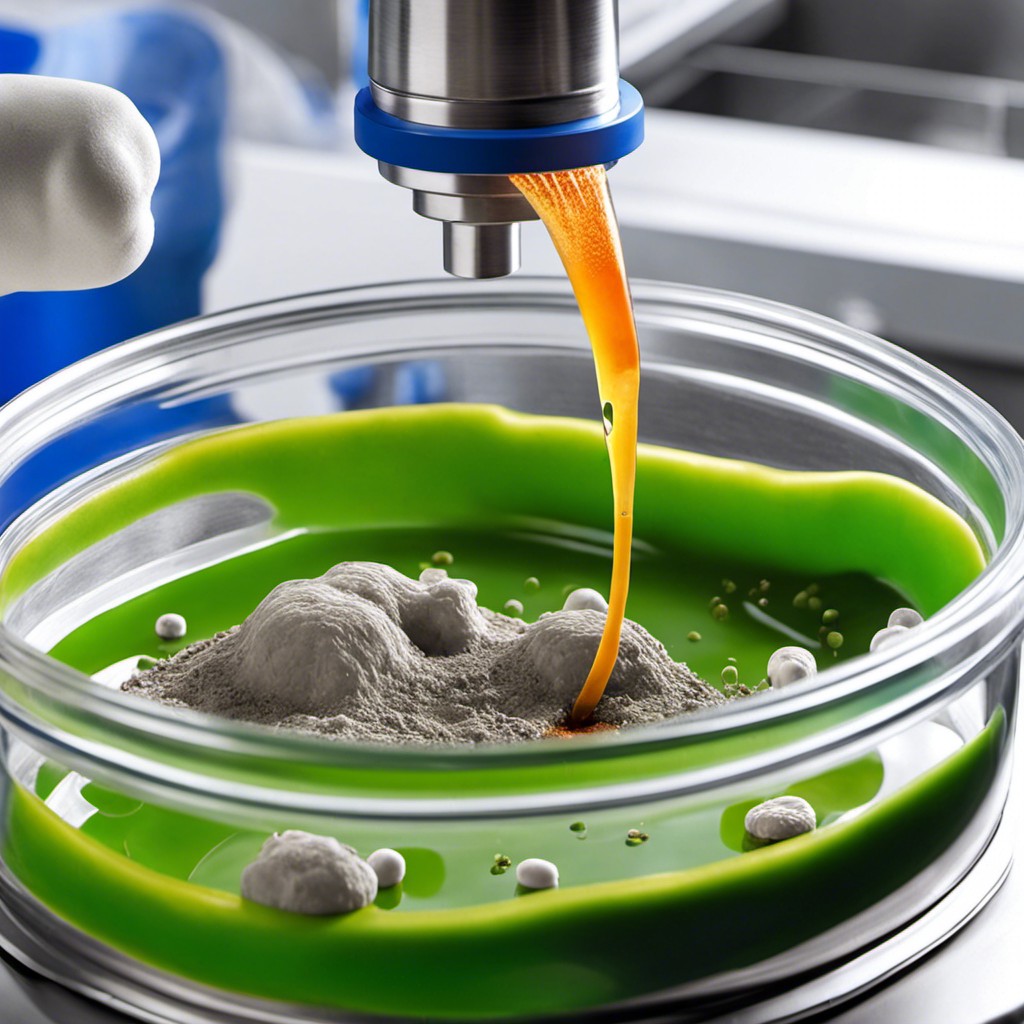
This innovative technique involves the use of bacteria, fungi, and other microorganisms to produce calcium carbonate or calcite crystals that bind soil particles together. The microbial cementation process has been found to be effective in stabilizing soils and creating durable building materials.
The benefits of using microbial cement are numerous. Firstly, it’s an eco-friendly alternative as it doesn’t require high energy consumption during production like traditional concrete does.
Secondly, this method can be used on-site with locally available resources which reduces transportation costs and carbon emissions associated with shipping building materials from far away locations.
Moreover, the resulting material is highly resistant to erosion caused by wind or water making it ideal for coastal areas where buildings are exposed to harsh weather conditions. Microbial cements have been shown to improve soil quality by increasing its strength while also reducing its permeability which helps prevent flooding in low-lying areas.
Nanotechnology in Cement Alternatives
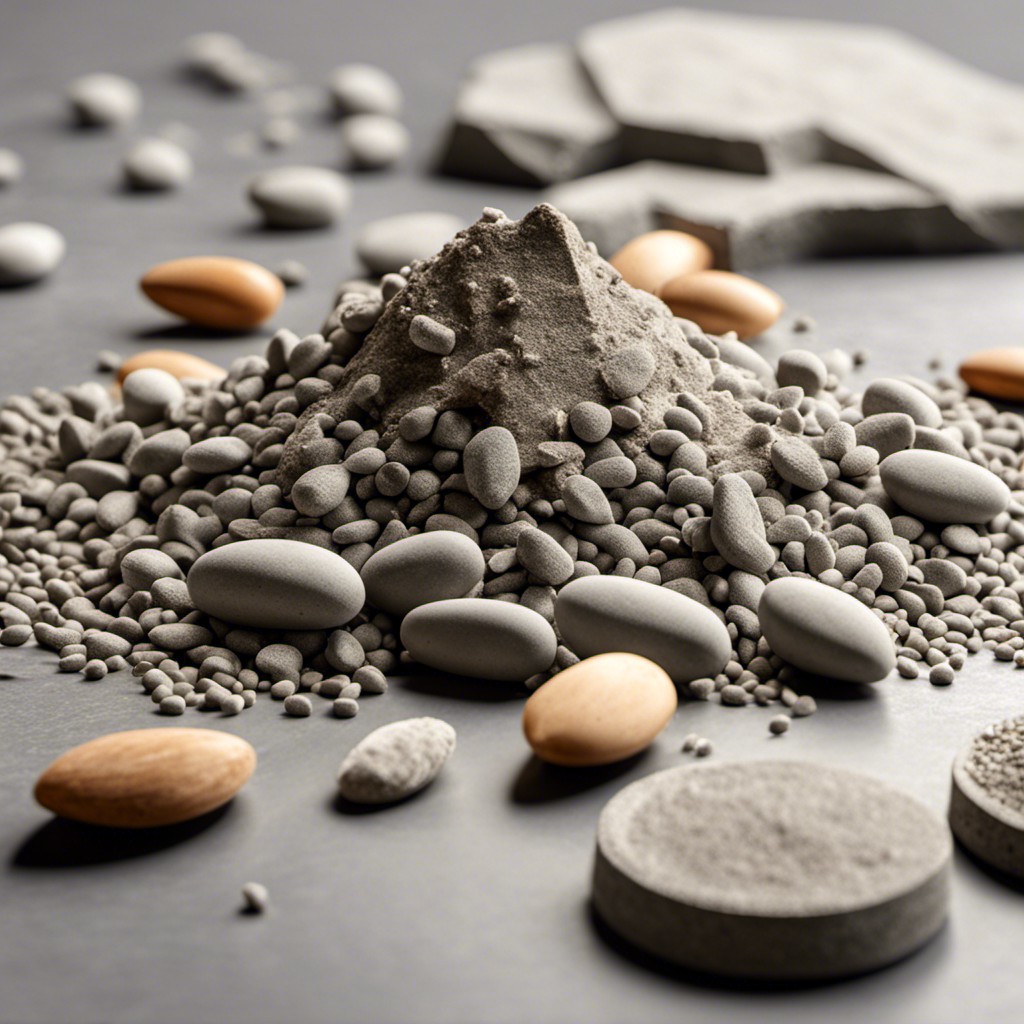
In recent years, researchers have been exploring the use of nanotechnology in cement alternatives as a way to improve their strength and durability while reducing their environmental impact.
One promising application of nanotechnology in cement alternatives is the use of nanoparticles such as carbon nanotubes or graphene oxide. These materials can be added to traditional concrete mixes to enhance its mechanical properties and reduce cracking.
Another area where nanotechnology shows promise is in developing self-healing concrete. By incorporating microcapsules filled with healing agents into the mix, cracks can be repaired automatically without human intervention.
Using nanomaterials in cement alternatives could lead to more sustainable and durable building materials that require less maintenance over time. While this technology is still relatively new and expensive at present times it’s worth keeping an eye on for future developments within eco-friendly construction practices.
FAQ
Is there a sustainable alternative to concrete?
Yes, sustainable alternatives to concrete include ferrock, ashcrete, timbercrete, and hempcrete, which require less carbon and utilize recycled waste materials such as steel dust and chaff.
Is there an eco-friendly cement?
Yes, an eco-friendly cement is Geopolymer concrete, which is more economical, durable, and environmentally friendly with a carbon footprint of just 10% compared to Portland cement.
What is the most sustainable cement?
The most sustainable cement is Green Cement, which uses a carbon-negative process and primarily employs discarded industrial waste materials such as slag from blast furnaces and fly ash for its manufacturing.
How do geopolymers compare to traditional cement in terms of environmental impact?
“Geopolymers have a significantly lower environmental impact than traditional cement, as they emit less CO2 during production.”
What innovative technologies are being developed for sustainable cement production?
Innovative technologies for sustainable cement production include carbon capture and storage, waste heat recovery systems, and low-carbon or carbon-negative cements.
Can recycled materials be effectively incorporated into cement blends for greener construction?
Yes, recycled materials can be effectively incorporated into cement blends for greener construction.
Recap