Last updated on
Here are the top alternatives to cement if you want to cut your carbon footprint and use sustainable materials in building or renovating your home. Read on!
Alternative cement options exist to cut down the use of calcium oxide (production of it has large energy emissions). These options allow us to use more eco-friendly materials in construction than traditional cement. Many green building companies switch to alternatives to decrease their energy consumption.
We cover the most popular alternatives to cement in this article. You can find more details about each option and whether you can use it.
Using Cement Alternatives to Create Concrete
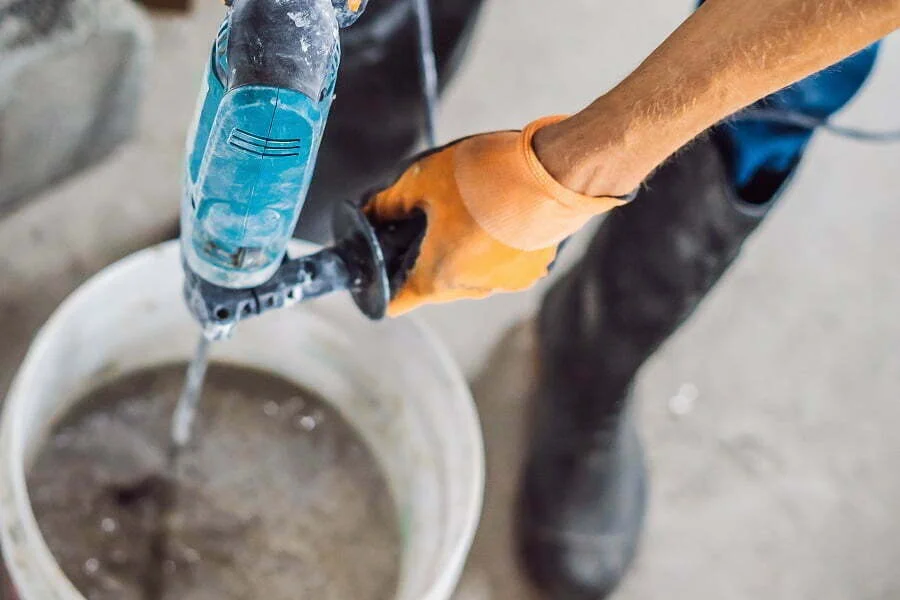
Traditional concrete is made by mixing sand, water, gravel, cement, and various other aggregates. Cement is the binding agent in concrete mixtures. When properly cured and dries, concrete forms a structure with impressive compressive strength, which is why it is commonly used in constructing bridges, buildings, roads, and other types of structures.
It is important to note that concrete is the second most widely consumed product globally, next to the water. This shows just how important it is. Unfortunately, the mining of calcium oxide and other minerals used to make cement, the critical constituent of concrete, is unsustainable. The natural reserves of these minerals are limited, while the energy used to produce cement is a crucial contributor to global warming.
That is why researchers have been working hard to find alternatives to cement. A number of them have been developed, and they produce impressive results. Most of these have already been adopted in the building and construction industry to create alternative concrete.
Pulverized Fuel Ash PFA (Fly Ash)
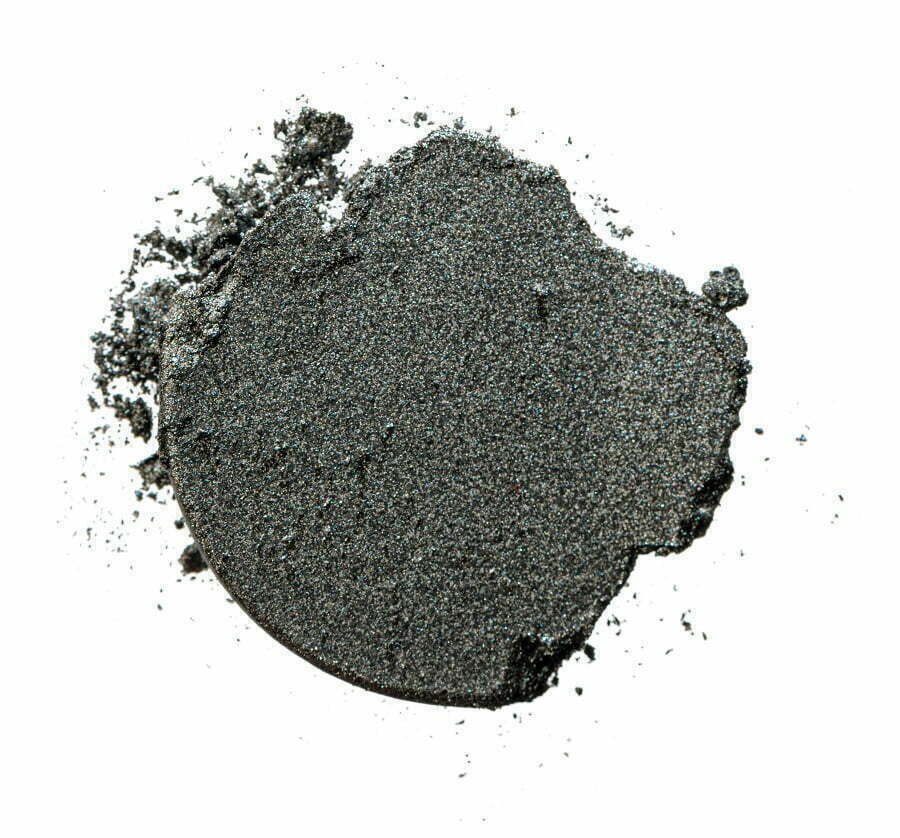
This is a by-product of power generation plants that use coal. It is first pulverized before the coal is burned to produce heat in power stations. About 18% of the pulverized coal powder forms fine glass spheres when burned. Three-quarters of these tiny glass spheres usually rise together with other by-products of coal combustion. These ash-like by-products are recovered from the exhaust fumes and used for various things, including making concrete known as fly ash or PFA.
Ground Granulated Blast-furnace Slag (GGBS)
In the manufacture of iron, slag usually rises to the top, leaving iron at the bottom. This slag is usually removed and quenched in water before ground into a fine powder. Like fly-ash, ground granulated blast furnace slag was initially considered waste and disposed of in landfills. However, it was discovered that the material could be used to replace up to 80% of cement in concrete, making it one of the best alternatives to cement.
Portland cement must still be added to the concrete mixture to obtain the best results. Usually, GGBS and portland cement can be mixed in the ratio of 40% to 60% up to 70% to 30%, making it a great alternative to cement.
Silica Fume
This is a by-product of the silicon manufacturing process. Silica fume contains particles as fine as smoke. The material can be used to make concrete either in a slurry or densified form. Due to the high cost of this cement alternative, the material is usually reserved for making concrete for aggressive environmental conditions and other special projects. The most widely used proportion of silica fume in the UK is about a tenth of the total cement content in concrete.
Limestone Fines
Portland limestone cement can be made from, among other things, limestone fines. Up to 10% of the total cement content in portland cement can be made of limestone fines.
Recycling of Materials
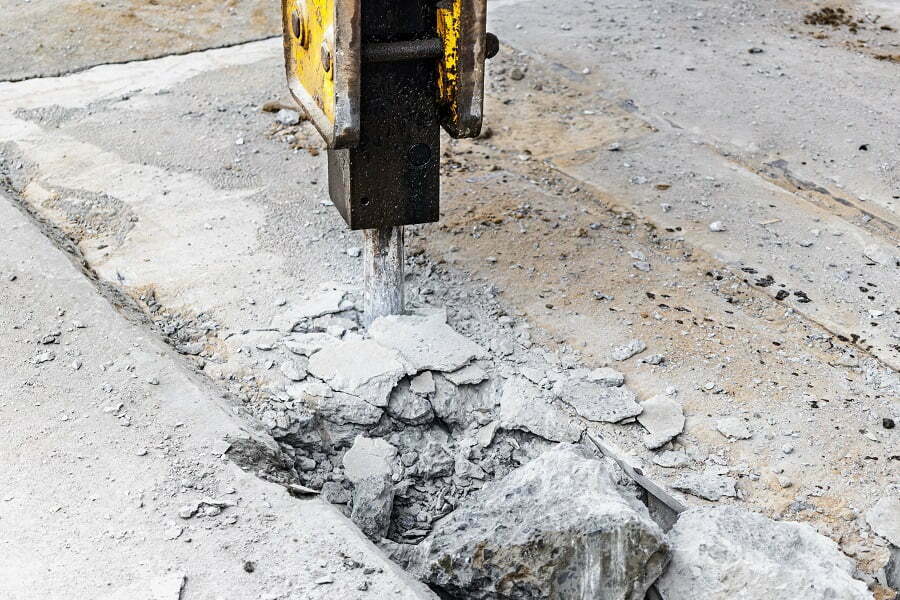
The key to creating a sustainable environment lies in recycling waste. This helps to reduce the amount of waste that eventually ends up in landfills. It also eliminates the need for more raw materials to manufacture products. When making concrete, it is possible to replace cement and other aggregates by recycling common waste products.
For instance, concrete debris can be recycled to reduce the amount of gravel, sand, and other aggregates used in making concrete. This helps reduce the amount of concrete waste dumped in landfills every year.
Consumer glass can also be recycled to replace some concrete aggregates. This not only increases the strength of concrete but also reduces the amount of glass waste that is buried in landfills every year.
Used tires can be used as fuel in cement manufacturing and eliminate the need to add iron oxide to cement as tires have some wire content that can provide the required iron oxide.
Plastics have a long life, are weather-resistant, and make an excellent replacement for aggregate material. They can be recycled many times without affecting the quality of the material. Recycled plastic can replace up to 20% of aggregate material in concrete.
Ferrock
Ferrock is an alternative component to cement that combines industrial waste, usually made from steel dust. It absorbs better than cement and makes stronger concrete.
Cements Based on Geopolymers
Geopolymer cement is a type of binding product known to harden at room temperature. The substance cures more rapidly than cement, usually in minutes rather than hours. Geopolymer cement can be made from industrial by-products and minimally processed natural products.
This type of cement is made by mixing water, fly ash, and a user-friendly alkaline reagent. Most geopolymer types of cement can cure and attain their maximum strength within 24 hours. This type of cement can help reduce carbon footprint and solve some durability issues of traditional concrete.
Biocements
These are made by mixing urea, calcium chloride, dry crude urease, and water. The last two ingredients are usually mixed on-site. Many other types of biocements are currently in use in the building and construction industry, and many others are under development. Biocements are eco-friendly and can effectively replace concrete.
Hemp Fibers
Hemp is an excellent renewable natural resource. Hemp seeds can be consumed and have exceptional nutritional properties. Edible oil can also be extracted from the hemp plant. The oil is also known to have medicinal properties. On the other hand, Hemp fibers can be used in the building industry. Originally, hemp fibers were combined with lime and water to make hempcrete, a concrete substitute. Nowadays, hemp stalks are used instead of fibers. Pozzolan, gypsum, and metakaolin are common types of binders used to make hempcrete.
Balterra Clay
Balterra clay is an unused by-product of bauxite mining. About 50% to 60% of limestone used in cement manufacturing could be replaced with Balterra clay. This can cut greenhouse gas emissions from cement manufacturing by up to two-thirds.
Carbonizing Cement to Decarbonize It
The production and use of cement account for 8% of global greenhouse gas emissions. This makes it one of the key contributors to global warming. It is hard to cut down on the 8% because cement depends on the building and construction industry. The best way to contain the emissions is through carbon capture. Carbon dioxide can be reutilized in various ways that can help reduce the impact of the cement industry. Any excess carbon can be stored for future use.
FAQ
Fly ash, ground granulated blast-furnace slag, and biocements are cheaper alternatives to cement.
Recycled materials, such as concrete debris, glass, plastics, and steel dust, are more sustainable alternatives to concrete.
Yes, it is possible to use alternatives to cement in construction. We cover all options in this article.
Recap