Last updated on
Explore the world of fiber-reinforced polymer alternatives as we dive into their various applications, benefits, and potential drawbacks in today’s ever-evolving construction industry.
Looking to revamp your home decor without breaking the bank? You’re not alone. As a budget-conscious homeowner, finding affordable alternatives to expensive materials is key to creating a stunning space that reflects your personal style.
And when it comes to decorative paneling, FRP (Fiberglass Reinforced Panels) have long been a popular choice for their durability and ease of installation. But what if we told you there are equally impressive alternatives out there? In this article, we’ll explore some of the best FRP alternatives that won’t compromise on style or quality – all while keeping your wallet happy.
Overview of FRP Alternatives
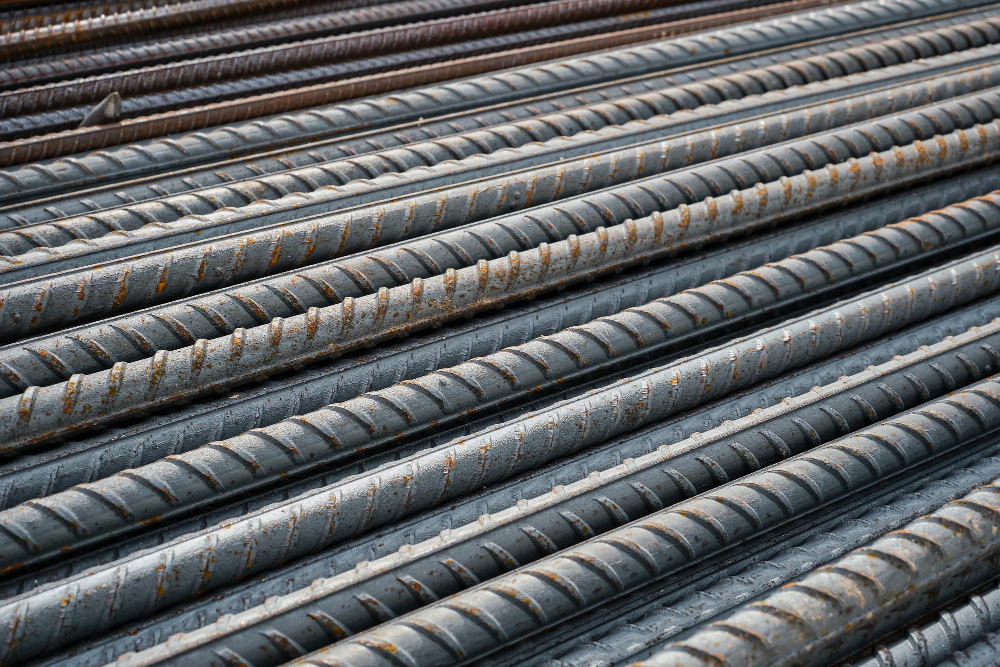
These materials range from natural fibers like bamboo to high-tech options like carbon fiber-reinforced polymer (CFRP). Each alternative has its own unique set of advantages and disadvantages, making it important to consider your specific needs before making a decision.
Some of the most popular FRP alternatives include steel reinforcement bars, basalt fiber-reinforced polymer (BFRP), glass fiber-reinforced polymer (GFRP), carbon fiber-reinforced polymer (CFRP), natural-fiber reinforced polymers such as bamboo or hemp-based composites. Hybrid Fiber-Reinforced Polymer is another option that combines two or more types of fibers in one material.
In addition to these composite materials, there are also innovative solutions such as textile reinforced concrete which uses fabrics instead of traditional steel reinforcements; engineered cementitious composites with improved ductility; geopolymer concrete made from industrial waste products; metallic-fiber reinforced concrete for added strength and durability; self-healing concrete with bacteria embedded within the mixtures that can repair cracks on their own.
Other non-composite options include PVC wall cladding systems designed specifically for hygienic environments where cleanliness is paramount. Interlocking multiwall panels provide an easy-to-install solution while dairy wall panels made by Duramax offer superior resistance against chemicals commonly found in agricultural settings.
Steel Reinforcement Bars
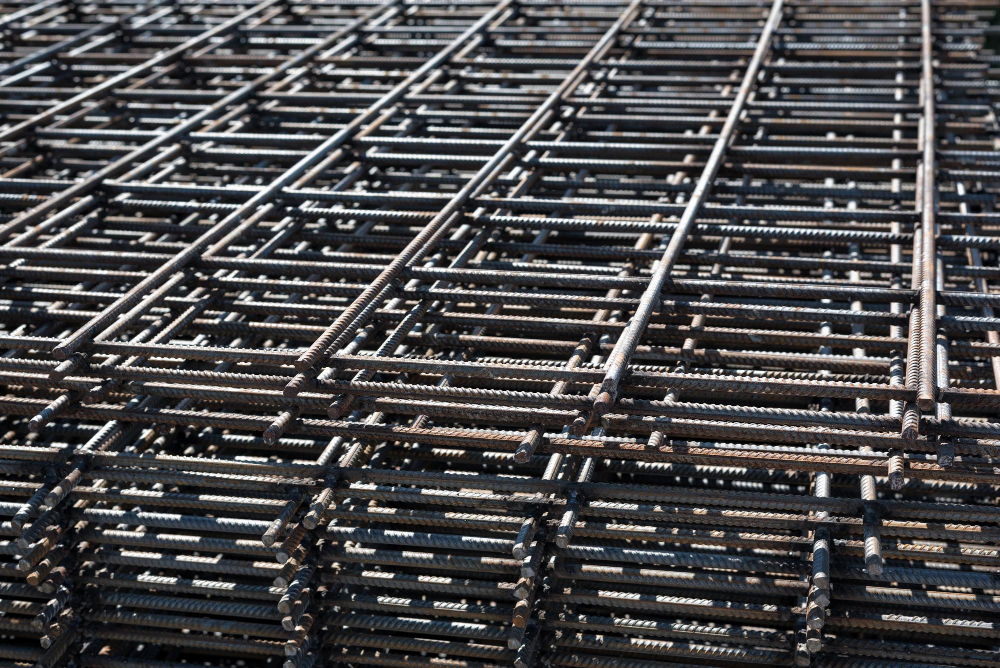
They have been used in construction for over a century and remain one of the most reliable options for reinforcing concrete structures. Rebar is made from carbon steel and can be found in various shapes such as round or square bars.
While steel reinforcement bars may not offer the same level of corrosion resistance as some FRP alternatives, they are still an excellent choice for projects that require heavy-duty support. Rebar is readily available at most hardware stores and can be easily cut to size on-site.
One potential drawback of using steel reinforcement bars is their susceptibility to rusting if exposed to moisture or chemicals over time. However, this issue can be mitigated by applying protective coatings or using stainless-steel rebar instead.
Basalt Fiber-Reinforced Polymer
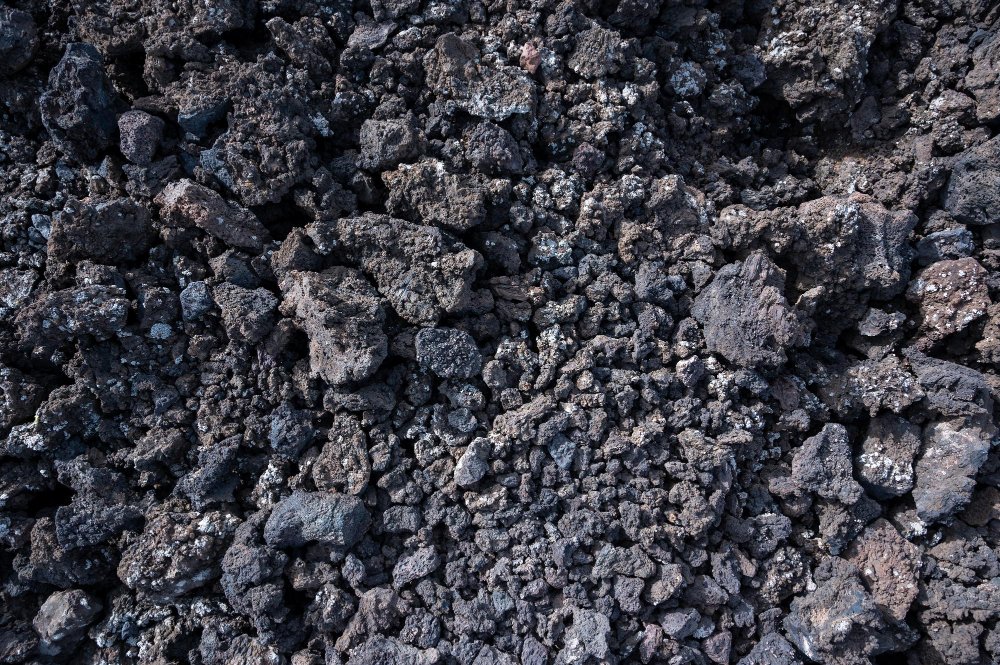
BFRP is made from basalt rock, which is melted at high temperatures and then spun into fibers. These fibers are then combined with a polymer resin to create composite materials that can be used for various applications.
One of the main advantages of BFRP over traditional FRPs like fiberglass or carbon fiber is its superior resistance to corrosion, making it an ideal choice for structures exposed to harsh environments such as bridges or offshore platforms. BFRP has excellent thermal stability and fire resistance properties.
Another benefit of using BFRP in construction projects is its sustainability factor – basalt rock being one of the most abundant natural resources on earth makes it an eco-friendly alternative compared to other synthetic materials.
Glass Fiber-Reinforced Polymer
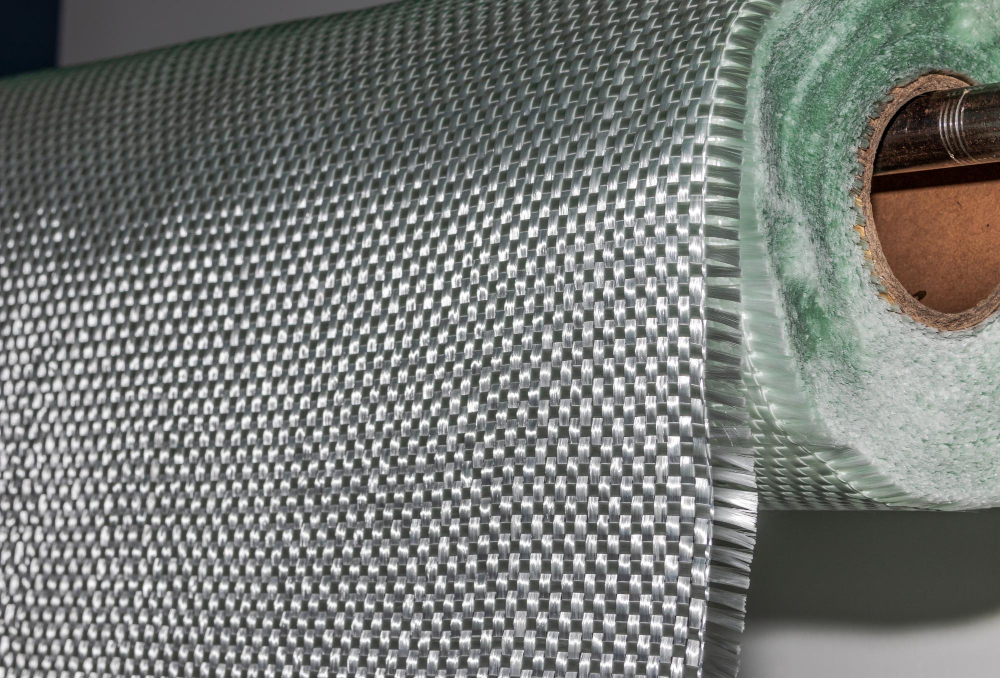
GFRP panels are made by reinforcing glass fibers with polymer resin, resulting in a lightweight and durable material that can be used for various applications. One of the main benefits of GFRP is its resistance to corrosion, making it an ideal choice for areas exposed to moisture or harsh weather conditions.
GFRP has excellent strength-to-weight ratio properties which make it suitable for use in construction projects where weight restrictions are critical. It also offers superior thermal insulation compared to other materials such as steel or aluminum.
Another advantage of using GFRP is its versatility in design options. The material can be molded into different shapes and sizes according to specific project requirements without compromising on structural integrity.
However, there are some potential drawbacks associated with using GFRPs such as their susceptibility to UV radiation damage over time if not properly protected from sunlight exposure during installation and maintenance procedures.
Carbon Fiber-Reinforced Polymer
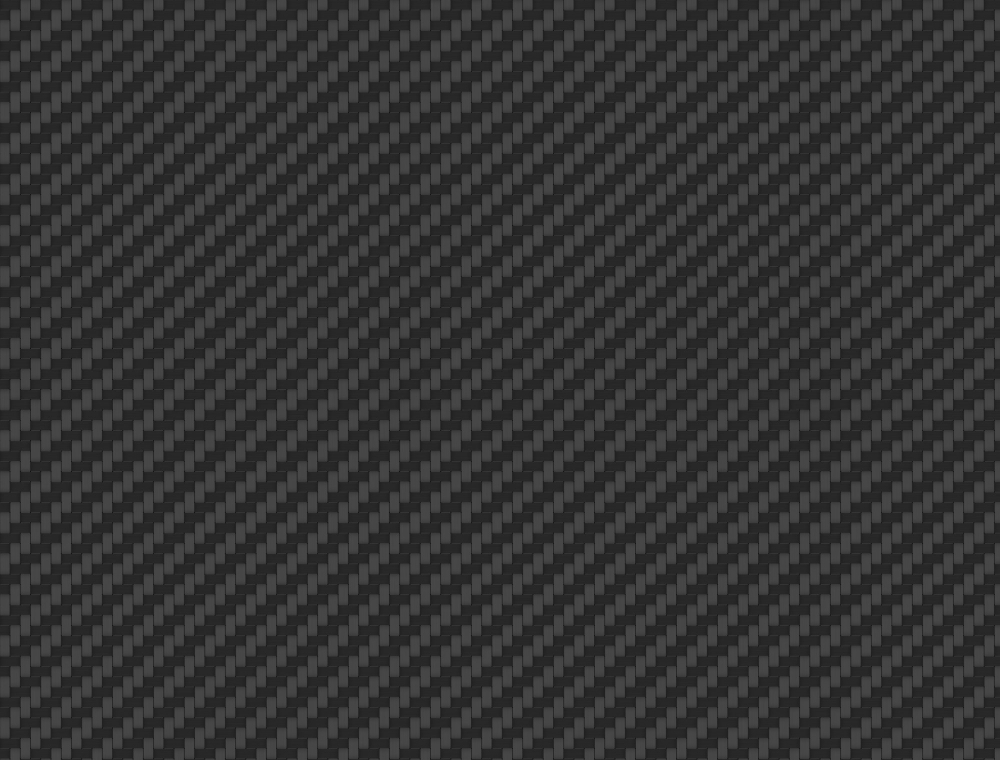
It has become increasingly popular in the construction industry due to its high strength-to-weight ratio, corrosion resistance, and durability. CFRP can be used for various applications such as strengthening concrete structures, repairing bridges or buildings, reinforcing steel beams or columns, and even creating lightweight furniture.
One of the main advantages of using CFRP over traditional materials like steel is its weight. Carbon fiber-reinforced polymers are much lighter than their metal counterparts while still maintaining comparable strength levels.
This makes them ideal for use in areas where weight reduction is critical such as aerospace engineering.
Another benefit of using CFRP is its excellent fatigue performance which means it can withstand repeated loading cycles without losing structural integrity over time. This makes it an attractive option for long-term projects where durability matters most.
However, there are some potential drawbacks to consider when working with carbon fiber-reinforced polymers including cost and difficulty in handling during installation due to their brittle nature compared to other FRPs like glass fibers reinforced polymer (GFRP).
Natural Fiber-Reinforced Polymer
These fibers are woven together to create a strong and durable material that can be used in various applications. NFRP has gained popularity in recent years due to its eco-friendliness and biodegradability.
One of the main advantages of using NFRP over traditional FRPs is its low cost. Natural fibers are readily available and inexpensive compared to synthetic materials like carbon or glass fiber.
They have lower density which makes them ideal for lightweight construction projects.
Another benefit of using NFRP is their sustainability factor – they’re renewable resources that don’t require high energy consumption during production processes unlike synthetic materials which contribute significantly towards environmental pollution.
However, there are some drawbacks associated with the use of natural fiber-reinforced polymer composites such as moisture absorption leading to swelling or warping if not properly sealed against water ingress; susceptibility to fungal growth when exposed continuously under humid conditions; limited strength properties compared with other types of FRPs making it unsuitable for certain applications where higher mechanical performance requirements exist.
Hybrid Fiber-Reinforced Polymer
HFRP can be used in various applications, including construction, automotive, aerospace, and marine industries.
One of the most significant advantages of HFRP is its ability to tailor the properties according to specific needs. For instance, combining carbon fiber with glass fiber can result in improved stiffness while maintaining cost-effectiveness.
Similarly, adding natural fibers such as jute or hemp can enhance impact resistance while reducing weight.
Another benefit of using HFRP over traditional materials like steel is its corrosion-resistant nature. Steel reinforcement bars are prone to rusting when exposed to moisture for an extended period – leading them towards failure eventually- whereas hybrid composites do not corrode even under harsh environmental conditions.
Textile-Reinforced Concrete
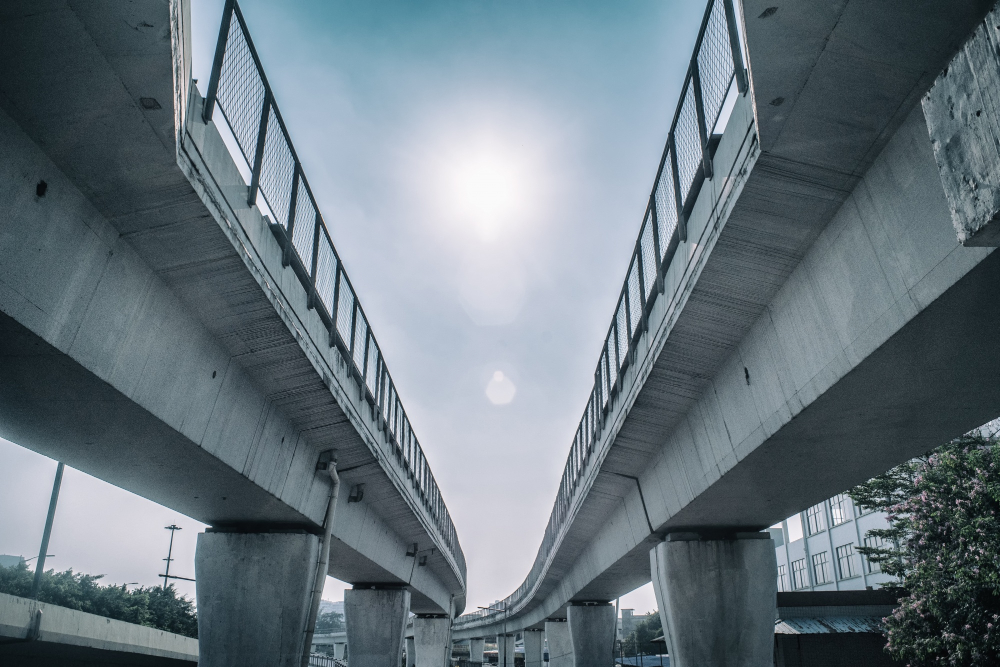
The use of textile reinforcement in concrete structures has been gaining popularity due to its high strength-to-weight ratio, durability, and flexibility. TRC can be used for various applications such as facades, roofs, bridges, tunnels and more.
The process involves impregnating woven or non-woven fabrics with cementitious materials to create a flexible yet strong reinforcement layer that is then embedded into the concrete matrix. This results in an improved tensile strength which helps prevent cracking under load.
One major advantage of TRC over traditional steel-reinforced concrete is its resistance to corrosion caused by exposure to harsh environmental conditions like saltwater or acidic substances. It offers greater design freedom since it can be molded into any shape desired without compromising on structural integrity.
However, there are some potential drawbacks associated with using TRCs such as higher costs compared to conventional reinforced concretes due to the need for specialized equipment during production processes; also limited availability may pose challenges when sourcing materials locally.
Engineered Cementitious Composites
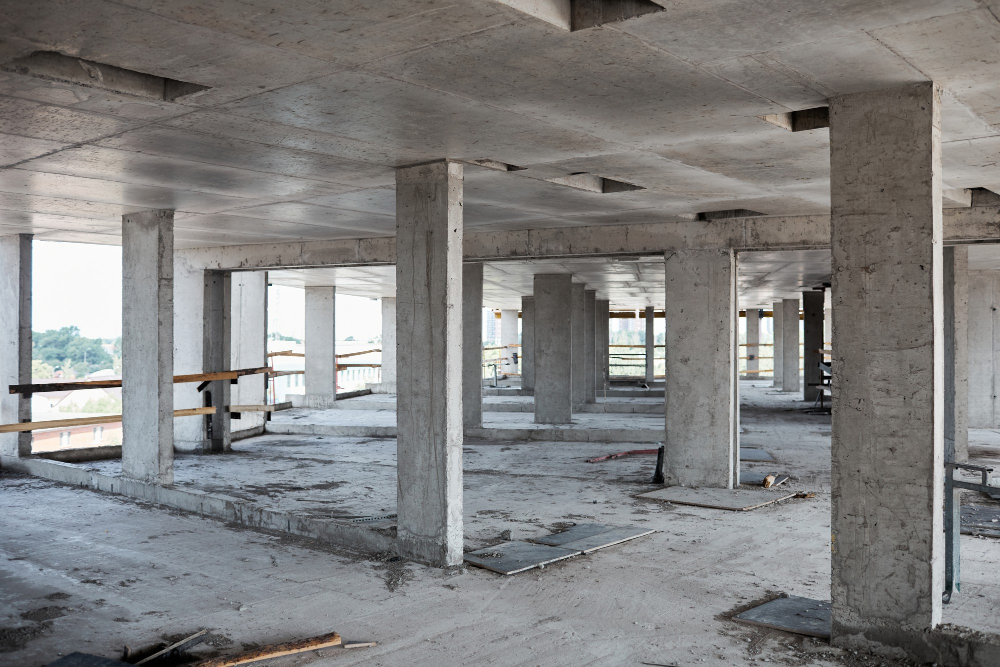
ECC is made up of cement, sand, water, and fibers such as polyvinyl alcohol (PVA), nylon or carbon. The addition of these fibers allows for greater flexibility in the material without compromising its structural integrity.
One major advantage of ECC over FRP is its ability to self-heal micro-cracks that may occur due to stress or environmental factors. This means less maintenance and repair costs in the long run.
Another benefit is its sustainability factor – ECC uses less cement than traditional concrete which reduces CO2 emissions during production while still maintaining high strength properties.
Fiber Reinforced Geopolymer Concrete
It is made by combining fly ash, an industrial waste product, with alkaline activators to create a binder that can be used as an alternative to traditional Portland cement. The resulting concrete has excellent mechanical properties and durability, making it ideal for use in construction projects.
One of the main advantages of Fiber Reinforced Geopolymer Concrete over traditional concrete is its environmental sustainability. By using fly ash instead of Portland cement, which requires significant amounts of energy and produces large amounts of carbon dioxide during production, geopolymer concrete significantly reduces greenhouse gas emissions.
In addition to being environmentally friendly, Fiber Reinforced Geopolymer Concrete also offers superior resistance against chemical attacks and fire damage compared to conventional materials. This makes it particularly suitable for use in harsh environments such as wastewater treatment plants or chemical factories.
Metallic Fiber-Reinforced Concrete
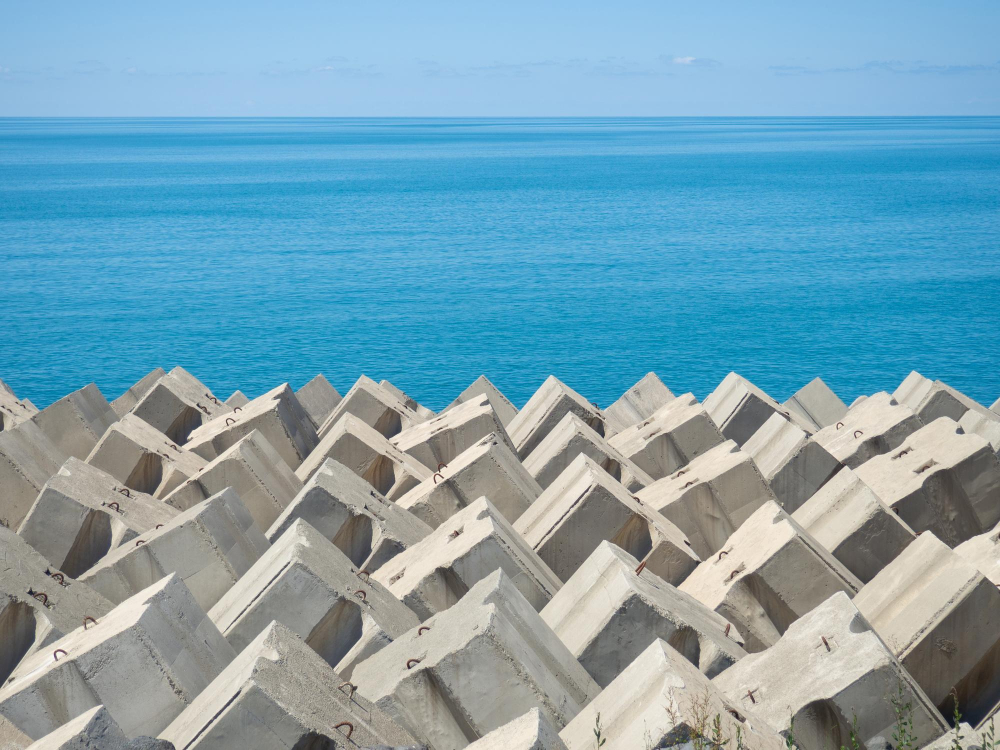
These fibers are made from materials such as steel, stainless steel, and aluminum. MFRC has been gaining popularity in recent years due to its high strength and durability compared to traditional concrete.
One of the main advantages of using MFRC is its ability to withstand heavy loads without cracking or breaking. This makes it an ideal choice for industrial applications where heavy machinery or equipment may be present.
Another benefit of using MFRC is its resistance to corrosion caused by exposure to harsh chemicals or environmental factors such as saltwater. This makes it a popular choice for construction projects near coastal areas.
However, one potential drawback of using MFRC is the cost associated with purchasing and installing metallic fibers into the concrete mix. Care must be taken during installation to ensure proper distribution throughout the mixture in order for it perform optimally.
Fiber Reinforced High-Ductility Concrete
This type of concrete is ideal for use in areas where high tensile strength and durability are required, such as bridges, tunnels, and other infrastructure projects.
The addition of fibers to the mix helps prevent cracking by distributing stress more evenly throughout the material. The result is a stronger, more durable product that can withstand heavy loads without breaking down over time.
One major advantage of Fiber Reinforced High-Ductility Concrete over traditional materials like steel or wood is its ability to resist corrosion. Unlike steel reinforcements which can rust over time leading to structural damage or failure; fiber-reinforced high-ductility concrete does not corrode even when exposed to harsh environmental conditions making it an excellent choice for long-lasting structures.
Nanotechnology in Concrete Reinforcement
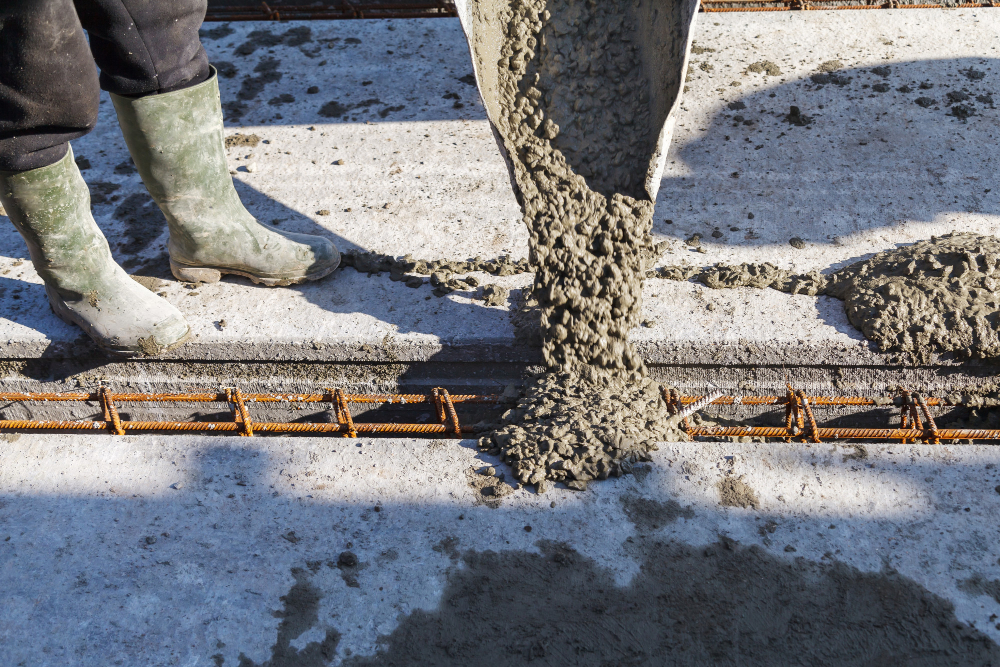
By incorporating nanoparticles into the mix, engineers can create a material that is stronger, more durable and resistant to environmental factors such as corrosion. Nanoparticles are incredibly small – around 1000 times smaller than a human hair – which means they can penetrate deep into the concrete matrix and fill any gaps or cracks that may form over time.
One of the most promising applications of nanotechnology in concrete reinforcement is carbon nanotubes (CNTs). These tiny tubes are incredibly strong – up to 100 times stronger than steel at one-sixth of its weight- making them an ideal candidate for reinforcing materials like cement.
CNTs also have excellent electrical conductivity properties which could be used in smart structures with embedded sensors.
Another application involves using nano-silica particles as an additive to traditional cement mixes. Nano-silica particles improve both compressive strength and durability by filling void spaces between larger aggregate particles within hardened cement paste.
Self-Healing Concrete
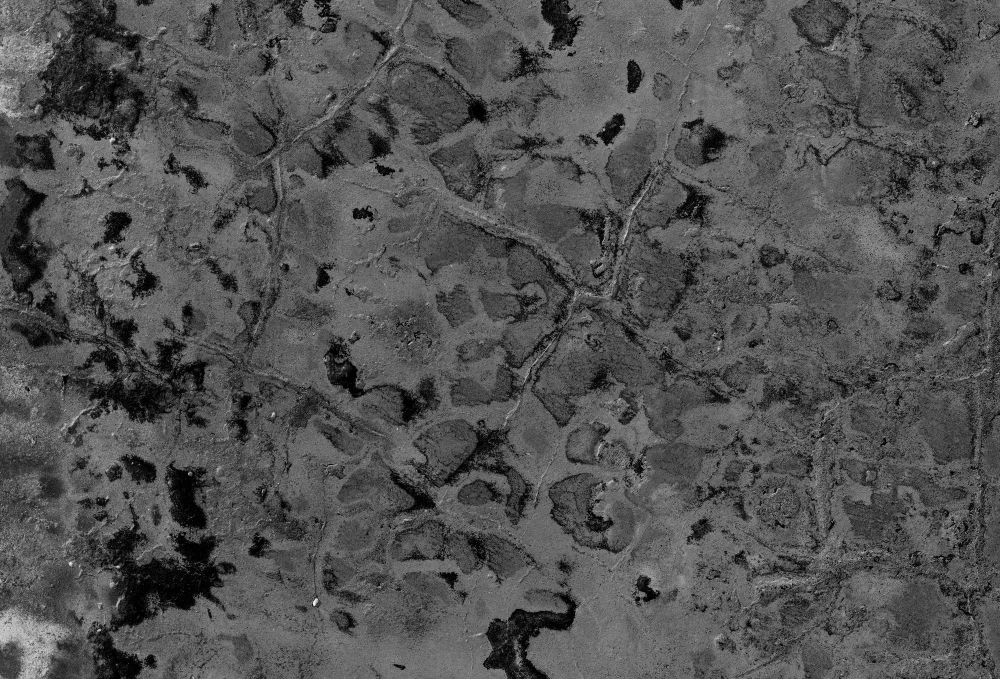
One of the biggest issues with concrete is that it can crack over time due to various factors such as temperature changes, moisture, and structural stress. However, researchers have been working on developing a solution to this problem – self-healing concrete.
Self-healing concrete contains bacteria or other microorganisms that are activated when cracks form in the material. These microorganisms produce calcium carbonate which fills up any gaps or cracks in the structure and restores its strength.
While still relatively new technology, self-healing concrete has shown promising results during testing phases and could potentially revolutionize how we approach construction projects going forward. Not only does this innovative material reduce maintenance costs by eliminating repair work for small-scale damage but also increases durability while reducing environmental impact through less waste production from repairs over time.
Dairy Wall Panels From Duramax
These panels are made of PVC material that is resistant to moisture, chemicals, and bacteria growth. They come in various colors and textures that can mimic the look of traditional wall materials like wood or stone.
Duramax dairy wall panels have a smooth surface finish which makes them easy to clean with just soap and water. Unlike FRP alternatives, they do not require any special cleaning agents or harsh chemicals which can be harmful to both humans and animals.
Moreover, these PVC wall cladding systems offer excellent insulation properties that help maintain stable temperatures inside the barns while reducing energy costs associated with heating or cooling.
Solid PVC Panels
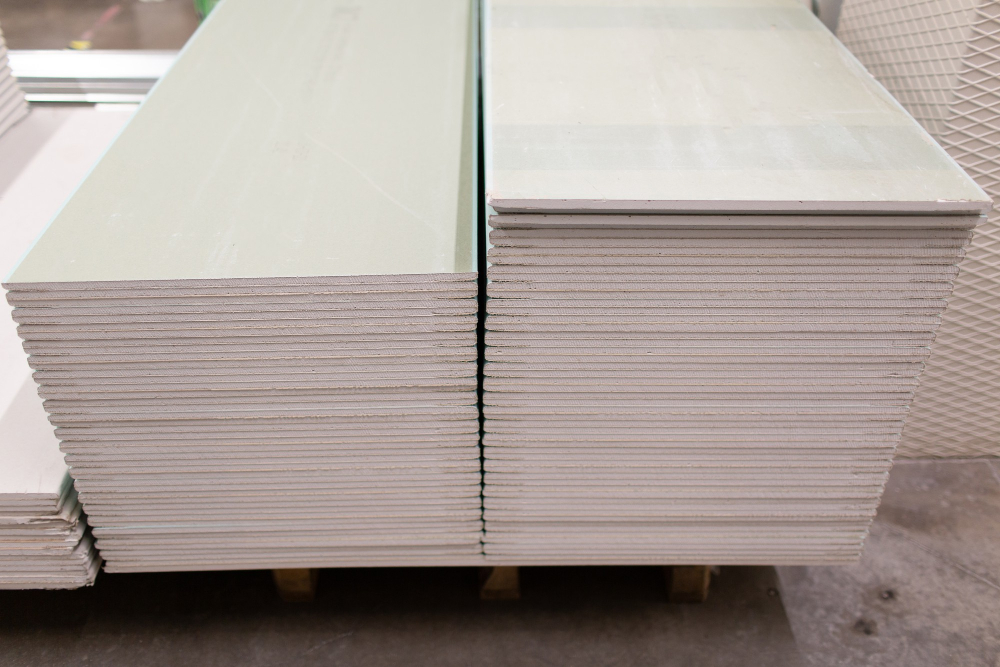
These panels are made from high-quality PVC resin, which makes them resistant to moisture, chemicals, and impact damage. They’re also easy to install and maintain – simply wipe them down with soap and water when needed.
One of the biggest advantages of solid PVC panels is their versatility in design. They come in a variety of colors, textures, patterns that can mimic natural materials like wood or stone without the added expense or maintenance requirements.
Another benefit is their durability over time; they don’t crack or warp under extreme temperatures like other materials might do. This means you won’t have to worry about replacing your wall paneling anytime soon!
Antimicrobial PVC Wall Cladding Systems
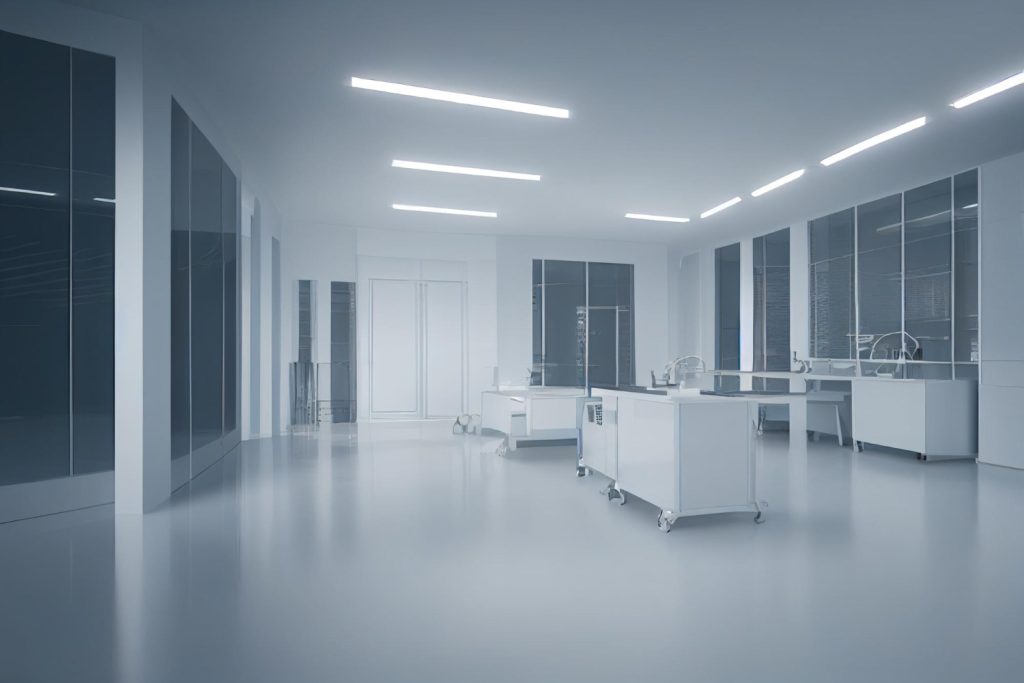
These panels are made from high-quality PVC material that has been treated with antimicrobial agents during the manufacturing process. This makes them resistant to bacteria and other microorganisms, making them ideal for use in hospitals, laboratories, food processing plants and other similar environments.
One of the key benefits of using antimicrobial PVC wall cladding systems is their ease of installation. They can be easily installed over existing walls or ceilings without any special tools or equipment required.
They require very little maintenance once installed – simply wipe down with a damp cloth as needed.
Another advantage is their durability – these panels are designed to withstand heavy traffic and frequent cleaning without showing signs of wear and tear over time. They also come in a variety of colors and finishes so you can choose one that best suits your decor needs.
When it comes to cost-effectiveness compared to traditional FRP paneling options; Antimicrobial PVC Wall Cladding Systems offer an affordable solution while still providing superior protection against harmful bacteria growth on surfaces within your home or business premises.
Interlocking Multiwall Panels
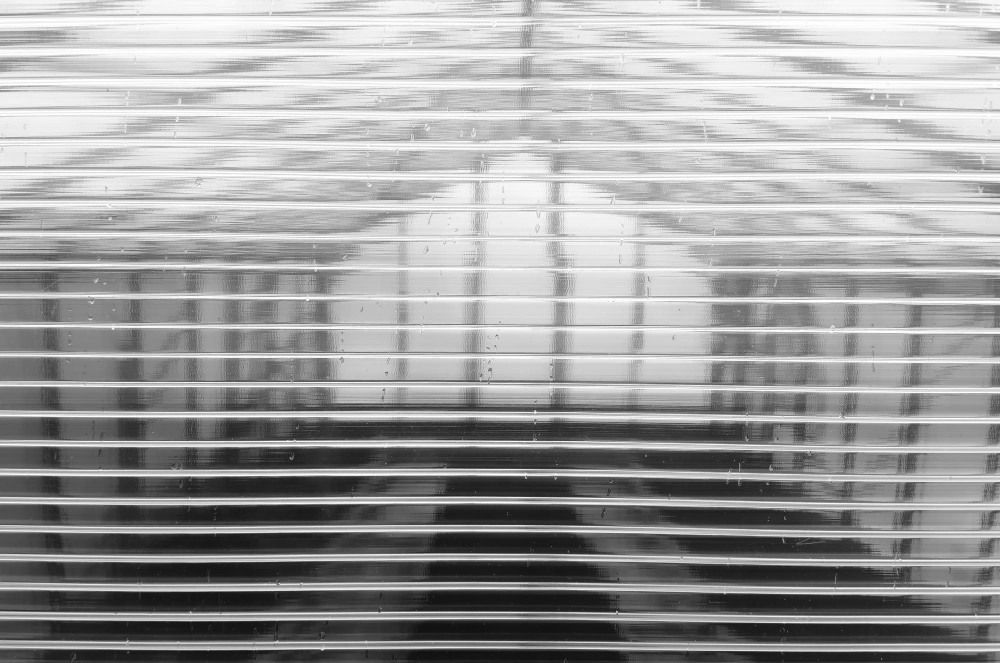
These panels consist of multiple layers of polycarbonate or acrylic sheets that are connected through interlocking channels, creating a sturdy and durable surface. They come in various colors, patterns, and textures to suit any design aesthetic.
One significant advantage of interlocking multiwall panels is their insulation properties. The air pockets between the layers provide excellent thermal insulation while allowing natural light to filter through – perfect for sunrooms or greenhouses.
Another benefit is their resistance to impact damage, making them ideal for high-traffic areas such as schools or hospitals where durability is crucial.
Installation is also straightforward with these types of panels since they can be cut on-site using standard tools like saws or drills without generating harmful dust particles like FRP does during installation.
Cost and Sustainability Analysis
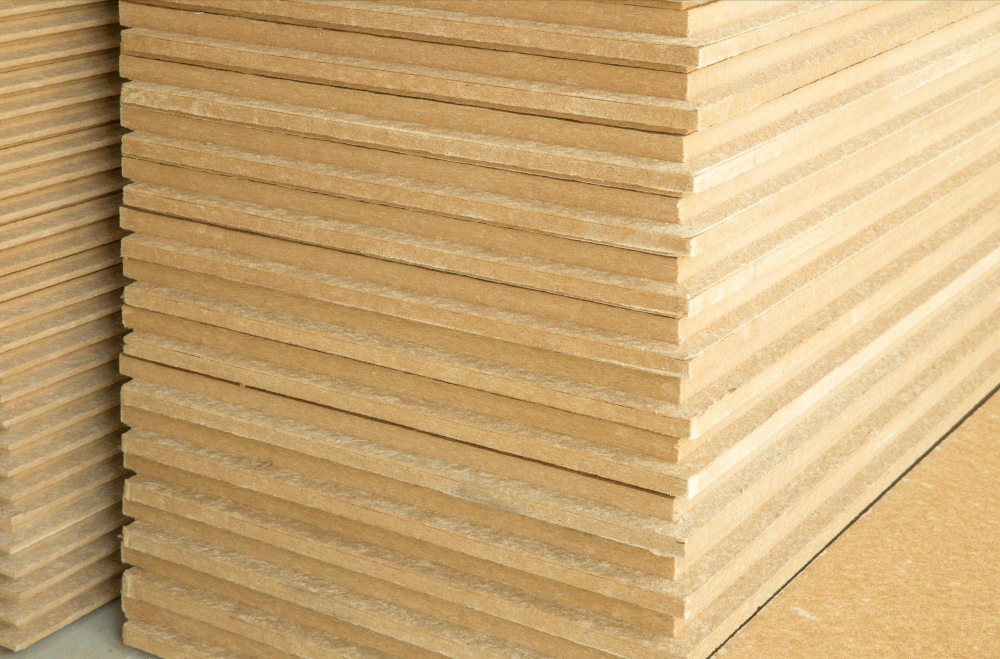
While some materials may have a lower upfront cost, they may not necessarily be the most sustainable option in the long run. On the other hand, investing in more eco-friendly options can lead to significant savings over time.
For instance, natural fiber-reinforced polymers such as hemp or flax composites are renewable resources that offer excellent strength-to-weight ratios and thermal insulation properties. They also require less energy during production compared to traditional FRPs made from non-renewable sources like fiberglass or carbon fibers.
Similarly, textile-reinforced concrete (TRC) is gaining popularity due to its high durability and low environmental impact. TRC uses fabric instead of steel reinforcement bars which reduces material waste by up 70%.
TRCs can last for decades without requiring any maintenance which translates into significant savings on repair costs over time.
While selecting an FRP alternative based solely on initial costs might seem like a good idea at first glance; taking sustainability factors into account will ultimately lead you towards making smarter choices for your home decor projects – both financially and environmentally speaking!
FAQ
What can I use instead of FRP?
An ideal alternative to FRP is Trusscore PVC panels, as they offer durability, water resistance, and are suitable for commercial projects.
Which is better NRP or FRP?
FRP is better than NRP as it offers higher impact resistance protection, making it more suitable for walls exposed to impacts from various sources.
Is PVC cheaper than FRP?
Yes, PVC is cheaper than FRP considering the long-term cost-effectiveness, and the additional labor and material expenses associated with FRP panels.
Why is FRP so expensive?
FRP is expensive due to its high labor costs and the need for additional materials such as wooden backers, glue, and fasteners, often requiring two laborers for installation.
What are the benefits of using fiberglass reinforced plastic (FRP) alternatives in construction projects?
FRP alternatives in construction projects offer benefits such as increased strength, corrosion resistance, reduced weight, and lower maintenance costs.
How do the durability and longevity of FRP alternatives compare with traditional FRP materials?
Durability and longevity of FRP alternatives often surpass traditional FRP materials due to improved material properties and reduced maintenance requirements.
In what applications might FRP alternatives prove to be more advantageous than using standard FRP?
In applications where weight reduction, corrosion resistance, improved durability, and design flexibility are desired, FRP alternatives can prove more advantageous than standard FRP.
Recap