Last updated on
Getting the lowdown on the volume of a concrete truck in yards is essential because it can significantly impact planning and execution of any construction project.
Key takeaways:
- Most standard concrete trucks can transport between 9 and 11 cubic yards.
- Concrete truck capacity is determined by weight limits and local laws.
- Different sizes of concrete trucks are available for various project needs.
- Compact trucks can carry around 2 to 4 cubic yards of concrete.
- Always discuss with your supplier to determine the best size for your project.
How Many Yards Can a Standard Concrete Truck Hold?
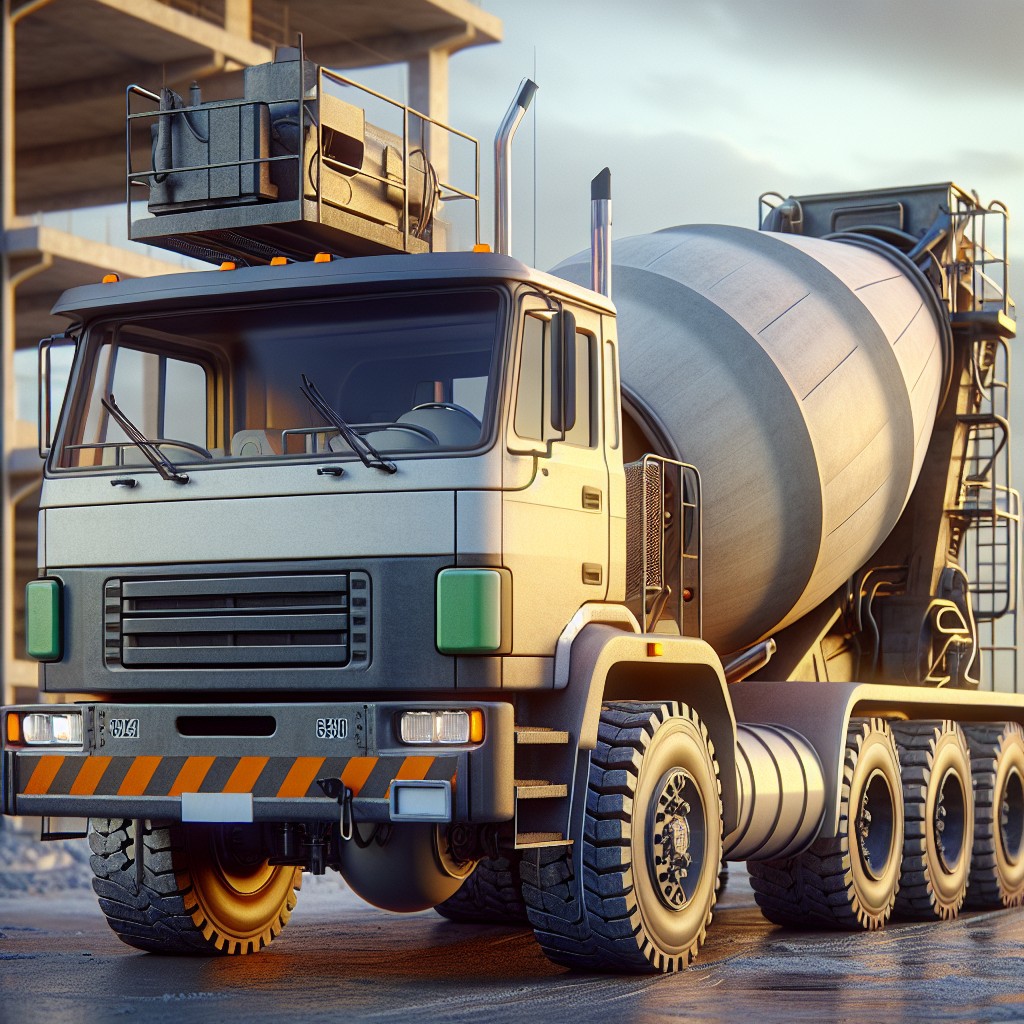
A typical concrete mixer truck is colloquially known as a “cement mixer.” The concrete is mixed and transported in a rotating drum on the back of the truck. But how much does one of these trucks actually hold?
- Most standard trucks can transport between 9 and 11 cubic yards of concrete.
- A cubic yard is a standard volume measure that fills a cube with sides of one yard.
- To put it in perspective, one yard is 3 feet, so a cubic yard is equivalent to a cube that is 3 feet wide, 3 feet long, and 3 feet tall.
- The capacity is determined partly by the truck’s weight limit and by local laws governing how much weight a truck can carry on public roads.
Considering these parameters, when planning a job requiring concrete, always discuss with your supplier to ensure you are ordering the correct amount. They can help calculate delivery requirements based on the volume of concrete you’ll need and the capacities of their mixer trucks.
Different Sizes of Concrete Trucks
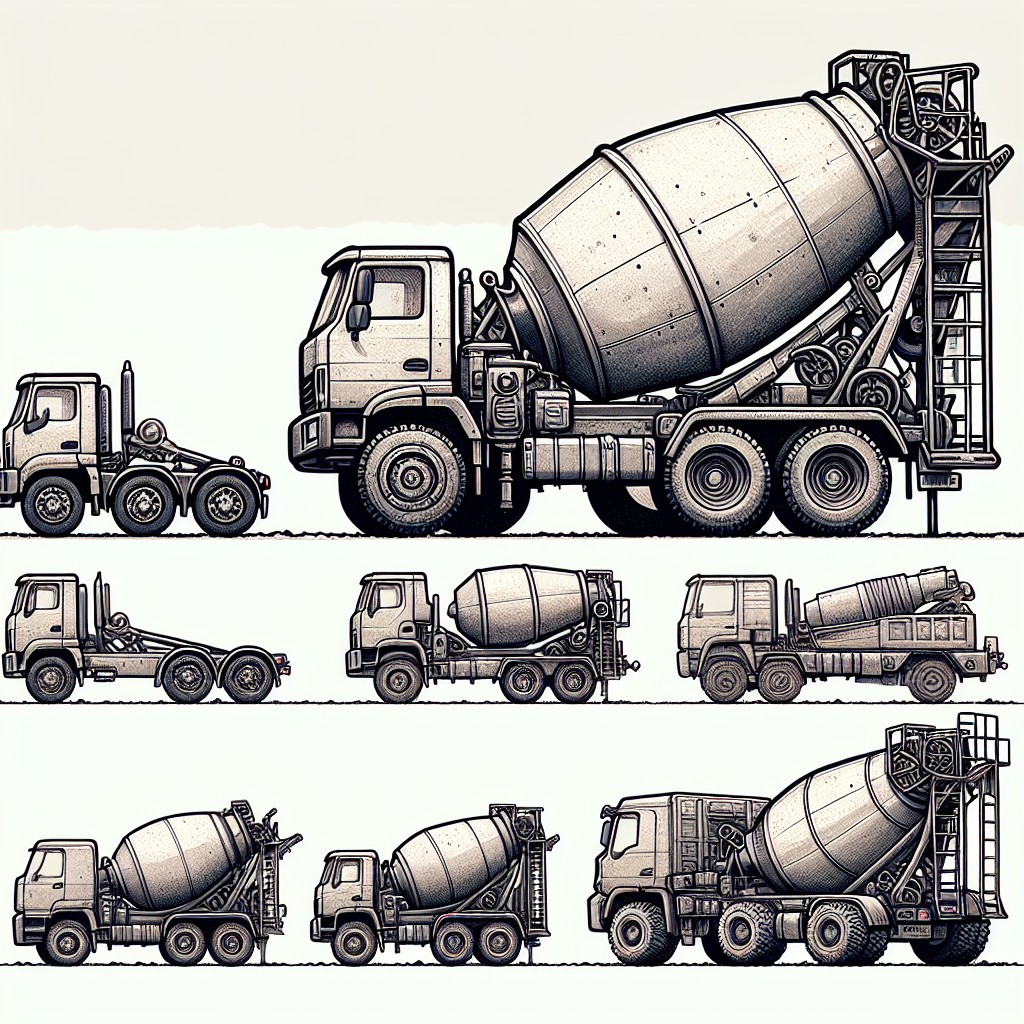
Concrete trucks, also known as cement mixers, come in a variety of capacities to suit different construction project needs. Here is a quick guide to understanding the common sizes:
– **Standard Mixer Trucks**: These vehicles typically have a capacity of around 8 to 14 cubic yards of concrete, with 10 cubic yards being the average. – **Mini Mixers**: Smaller projects may utilize mini mixers that can carry approximately 3 cubic yards. – **Large Volume Mixers**: For extensive construction tasks, mixers are available that can haul 15+ cubic yards.Keep in mind the legal weight limits for roads and bridges, as this can restrict the maximum loaded capacity of a concrete truck regardless of its physical volume capacity. Always coordinate with your supplier to determine the best size for your particular project’s requirements.
Variations and Regulations: The Plot Thickens
Concrete trucks come in various sizes, capable of holding different volumes. Typically, standard mixers can carry around 10 cubic yards of concrete. However, not all trucks you’ll encounter on the road or at job sites are standard.
- Depending on the construction requirements, compact trucks able to navigate tighter spaces may be used, usually with a capacity ranging from 2 to 4 cubic yards.
- Legal weight restrictions also influence truck sizes. Roads have maximum allowable weights; this dictates the maximum amount of concrete a truck can transport without exceeding these limits.
- Overweight trucks are subject to fines or may be prohibited from using certain roads, impacting the efficiency and cost of concrete delivery.
- Lastly, the design of each truck, whether rear discharge or front discharge, further affects its carrying capacity and operational nuances, such as how concrete is poured upon arrival at the job site.
Understanding these variables is key in estimating the number of trucks needed for your project and in ensuring compliance with local and federal transportation regulations.
How Much Concrete Do You Need?
Calculating the amount of concrete required for your project is essential before ordering from a concrete truck. Here’s how to estimate the volume:
1. Measure the Length, Width, and Height: Use feet as a standard unit when measuring the area to be poured. Length times width times height equals volume in cubic feet.
2. Convert to Cubic Yards: Since concrete is typically sold by the cubic yard, convert your volume from cubic feet to cubic yards by dividing by 27 (the number of cubic feet in one cubic yard).
3. Account for Overages: It is prudent to add a buffer, generally 10%, to accommodate for spillage, depth variations, or miscalculations in your initial measurements.
4. Consult with Professionals: If you’re unsure about your calculations, consult with a concrete contractor or supplier who can provide guidance and ensure you order the correct amount.
What Are the Different Types of Concrete Trucks With Respect to Size?
Standard transit mixers typically come in two main sizes: a 6-cubic yard capacity and a 10-cubic yard capacity. For larger projects, a 10- or 11-cubic yard truck is used, while smaller projects may only require a 6-cubic yard truck.
In addition, front discharge and rear discharge trucks vary in size. Front discharge trucks are generally larger, with capacities ranging from 10 to 15 cubic yards. They provide the advantage of better visibility and control for the driver.
Rear discharge trucks, on the other hand, tend to range from 9 to 11 cubic yards in capacity. These require external chutes for concrete placement and are more common in residential projects.
It’s also important to note maxi-trucks, which have capacities of up to 12.5 cubic yards, ideal for substantial commercial jobs, and mini mix trucks designed for smaller loads, usually around 3 cubic yards, perfect for tight spaces or smaller pour requirements.
The size of the truck to be used is usually determined by the volume of concrete required for the job and the access to the project site.
How Does Concrete Not Harden in a Truck?
To ensure concrete remains workable during transport, concrete mixer trucks leverage the principles of motion and specific admixtures:
- The constant rotation of the drum mixes the ingredients and prevents the concrete from hardening.
- Admixtures, such as retarders, are added to the mixture to slow down the chemical process of hydration, which is the reaction that causes concrete to harden.
- Water is carefully measured and mixed to control the setting time, with adjustments made on-site if necessary.
- In colder climates, heaters within the drum warm the mix, which helps to manage the curing process during travel.
- The timing is crucial; from loading to discharge, the process is closely monitored to ensure concrete is delivered within a workable time frame, usually within 90 minutes to avoid overhydration and setting.
What Is the Setting Time of Concrete?
Setting time for concrete hinges on a mix of factors, including weather conditions, water-cement ratio, and the presence of admixtures. Typically, the initial set begins around 30 to 45 minutes after mixing, but this is not when it’s firm enough to bear weight. That stage, known as final set, may take up to 6 to 8 hours. High temperatures often accelerate the process, while cold weather can significantly delay it. Admixtures are frequently used to manipulate these times to suit specific project needs. It’s crucial to monitor setting times to ensure the proper handling and finishing of concrete, thus ensuring its strength and durability.
How Long Can It Take to Pour 10 Yards of Concrete?
The duration of pouring 10 yards of concrete hinges on several aspects including the complexity of the project, accessibility of the pour site, and manpower available. Typically, with a professional crew, the pour process for this amount can typically be completed in one to two hours.
Factors affecting this time frame include:
- Site Accessibility: If the truck can directly access the site, the process is expedited. Otherwise, additional equipment like concrete pumps or wheelbarrows may be necessary, extending the time needed.
- Project Complexity: Simple projects, like slabs for sheds, take less time compared to intricate pours such as winding walkways or steps that require detailed forms and finishing.
- Manpower: More hands on deck can significantly reduce the pour time. A well-coordinated team can streamline the process, ensuring a quicker and more efficient pour.
- Weather Conditions: Favorable weather speeds up the process, whereas extreme conditions like high winds or temperatures can slow it down due to the effects on concrete setting times.
- Preparation: Having all forms and sub-base ready and ensuring the crew is briefed on the pour plan avoid delays once the truck arrives.
Remember, optimal planning and coordination are crucial to maximizing efficiency during the pour.
How Much Is a Cubic Yard of Concrete?
Understanding the cost of a cubic yard of concrete is crucial when planning any construction project. Price is influenced by factors such as the concrete grade, location, season, and delivery fees.
On average:
- Material Costs: A basic cubic yard of concrete typically ranges from $80 to $120. However, specialized mixes for specific applications may cost more.
- Delivery Fees: Concrete delivered to your site may have additional charges based on the distance from the plant.
- Minimum Order: Some companies impose minimum order requirements, influencing the overall cost.
- Supply and Demand: Seasonal changes and local demand can cause fluctuations in pricing.
For an accurate estimate, it’s always best to contact local suppliers and request a quote based on your project details.
How Will I Be Charged for the Concrete?
Concrete is typically charged by the cubic yard, with the cost varying based on the grade (strength) of concrete you order. Additional factors that could impact the total cost include:
- Delivery Fees: These are often applied to your bill to cover the transportation of the concrete from the plant to your site. The distance covered may affect this fee.
- Minimum Load Charge: Some concrete suppliers charge for a full truckload even if you order less. It’s advisable to confirm the supplier’s policy regarding partial loads.
- Environmental Fees: If your project requires the disposal of concrete or uses specific additives, you might encounter environmental fees.
- Weekend or After-Hours Service: Orders outside of standard business hours could incur extra charges.
- Short Load Charges: If your project doesn’t require a full truckload, some companies offer short load services for a small quantity but often at a higher rate per cubic yard.
Always inquire about what is included in the quote you receive to avoid surprises on the billing statement.
What Do I Need to Have Done When the Concrete Arrives?
Ensure the site is accessible with a clear path for the truck, free from obstructions like low-hanging wires or narrow entryways. Proper access ensures the truck can maneuver close to the desired pour location, which is crucial to avoid additional equipment or labor costs to move the concrete from the truck to the site.
Have your forms built and properly secured. These will shape and contain the concrete once poured, so double-check for sturdiness and accuracy in dimensions.
Confirm that any required reinforcements, such as rebar or wire mesh, are in place and properly tied down. This step is essential to the structural integrity of the finished concrete.
Keep your tools and finishing supplies at the ready. Items such as shovels, rakes, screeds, and floats should be on hand to spread and smooth the concrete immediately after pouring.
Ensure you have an adequate workforce prepared. The size and complexity of the project will dictate the number of people needed to help with the pour and finish work.
Lastly, have a contingency plan for weather conditions or unexpected delays. Concrete sets faster in hot weather and slower in cold, so be prepared to adapt your schedule and protect the concrete if necessary.
What Will the Concrete Company Need to Know?
To ensure a smooth concrete delivery process, the company will need certain details:
- Project site address for accurate delivery.
- Type of concrete mix required, which depends on the project’s needs, such as a driveway, foundation, or patio.
- Total volume of concrete in cubic yards. It’s vital to accurately calculate the amount needed, as both shortages and excess can cause problems.
- Delivery date and time preference, coordinated to match the project schedule.
- Specific delivery instructions such as the preferred route or unloading area to avoid delays or access issues.
- Information about the pour site, including the accessibility for the truck, the presence of obstructions, and the need for additional equipment like concrete pumps.
- Any special additives or finishes needed in the mix for enhanced durability or aesthetic purposes.
By providing clear and thorough information in these areas, you can assist the concrete company in preparing adequately for your job, leading to a seamless operation on pour day.
Concrete Cost Per Yard
The price per cubic yard of concrete varies depending on a few key factors: your geographic location, the current price of raw materials, and the total amount you purchase.
Typically, as of early 2023, you can expect to pay between $120 to $150 for a cubic yard of standard ready-mix concrete.
Keep in mind, the cost can escalate to $170 or more for higher-grade concrete mixtures that contain additives for accelerated curing, additional strength, or for low-shrinkage properties.
Complex mixes designed for specific environmental factors or those that include reinforcements like mesh or fiber could also bump up the price.
Moreover, if your project is located far from the concrete plant or requires any specialty services such as overnight pouring or rapid delivery, additional fees could be applied by your concrete supplier.
Remember, bulk orders usually attract discounts, so the more you order up to the truck’s full capacity, the more cost-effective your project becomes.
It’s always a good idea to speak directly with your supplier to get an accurate quote based on the specifics of your project and to inquire about any possible discounts or additional charges that might apply.
Short-Load Concrete Prices
Short-load concrete refers to concrete delivered in quantities less than a full truckload, which is typically less than 10 cubic yards. Here’s how pricing works for these smaller loads:
- Volume Based: You’ll be charged based on the volume of concrete ordered. As the quantity decreases, the price per cubic yard increases due to delivery and operational costs.
- Minimum Load Fees: Expect to pay a minimum load fee to cover the costs of operating the truck, regardless of the amount of concrete you order.
- Delivery Fees: Some companies impose a delivery fee for short loads to account for the driver’s time and fuel.
- Overtime Charges: If your project requires additional time to offload the concrete, overtime fees may apply, typically calculated on an hourly basis after a designated period.
- Partial Load Charges: There might also be a surcharge for ordering a partial load to maximize the efficiency of the truck’s capacity.
Comparing quotes and understanding the full breakdown of fees will help ensure that you’re getting the best deal for your short-load concrete needs.
Ready-Mix Concrete Prices
Ready-mix concrete prices are influenced by several factors including the quantity required, the concrete’s mix design (which affects the strength and durability needed for your project), and your location, as delivery costs can vary.
- Cost per cubic yard: On average, expect to pay between $120 to $150 for a cubic yard of ready-mix concrete.
- Delivery fees: These can significantly increase the total price, especially for small orders. Some companies charge a “short load” fee for orders under a certain yardage.
- Seasonality: Prices can fluctuate seasonally, with potential for higher rates during busy construction months.
- Additional charges: Be mindful of extra costs for additives like accelerators or colorants, and extended on-site waiting time if your project delays the pour.
Questions to Ask Your Concrete Contractor
Before committing to a concrete contractor, it’s crucial to clarify details to ensure your project’s success. Here’s what you should ask:
- What is your experience with projects similar to mine? Inquire about relevant experience to gauge the contractor’s ability to handle your specific project.
- Can you provide references or photos of past work? Reputable contractors will have proof of their craftsmanship and satisfied customers.
- How long will the project take from start to finish? Setting expectations for the project timeline helps plan accordingly.
- What is the schedule for payments? Understand the payment milestones before work begins to avoid confusion.
- Do you handle obtaining necessary permits? Confirm whether the contractor will manage the permitting process or if it’s your responsibility.
- What type of concrete mix do you recommend? The contractor should suggest the appropriate mix based on the project’s requirements.
- What is included in the quote? Ensure the quote covers all aspects of the job, such as prep work and cleanup.
- How do you address potential issues such as weather delays? Learning the contractor’s contingency plans will indicate their preparedness for unexpected events.
Asking these questions ensures transparency and quality, leading to a smoother project flow.
Prep Work Before Pouring Concrete
Before the arrival of the concrete truck, ensuring the site is ready is crucial for a successful pour. Start with clearing debris and removing any vegetation from the area which can interfere with the concrete’s integrity. Compacting the soil provides a stable base, preventing uneven settlement later on.
Formwork, made of wood or metal, is essential and should be strong enough to hold the concrete; this defines the shape and supports the pour.
It’s also important to consider water drainage – slope the site away from structures to prevent water pooling. Lastly, install reinforcement like wire mesh or steel rebar to minimize cracking and enhance the strength of the slab.
By attending to these preparatory steps, you create the groundwork for a long-lasting and sturdy concrete project.
Grading
Before the arrival of the concrete truck, proper grading establishes a level base and sets the stage for adequate drainage. Consider the following:
- Grading involves slight sloping away from structures for water runoff.
- Elevation differences are smoothed out to prevent pooling.
- A consistent compaction across the site ensures a uniform foundation.
- Make use of string lines or laser levels for accuracy.
- Check local codes for specific grade requirements to comply with regulations.
- If you’re unsure about how to grade your site correctly, consult a professional. Proper site preparation reduces the risk of cracks and foundation issues.
Subbase
A well-prepared subbase is key to the longevity and stability of the poured concrete. The subbase is the layer of material upon which the slab is laid, providing a stable surface and controlling the drainage:
- Typically composed of gravel or crushed stone, the subbase should be spread to a uniform thickness.
- Compaction is crucial; the subbase must be compacted to provide a solid foundation, reducing the chance of settlement and preventing the concrete from cracking.
- A moisture barrier, often in the form of a polyethylene sheet, is sometimes placed over the subbase to prevent moisture from seeping up from the ground into the slab.
- The subbase depth can vary depending on the project’s requirements, with deeper layers needed for heavier loads.
- Proper subbase preparation ensures that the ground beneath the concrete has adequate drainage, preventing water from pooling under the slab, which could cause erosion or frost heave in colder climates.
Attention to these details will significantly enhance the performance of your concrete project, providing a firm foundation for whatever is built upon it.
Concrete Reinforcement
To enhance the structural integrity of poured concrete, reinforcement is a key component. Here’s what you need to know:
1. Rebar: Steel bars, commonly known as rebar, are frequently embedded within the concrete to provide additional tensile strength.
2. Wire Mesh: For slab projects, wire mesh offers effective reinforcement, preventing cracking over time and helping to distribute weight evenly.
3. Fibers: Modern mixes often include polypropylene fibers that mitigate the formation of micro cracks as concrete cures.
4. Post-tension cables: Primarily used in large slab applications, these cables are tensioned after the concrete has cured to give extra support where needed.
5. Placement matters: Reinforcement should be placed at the right depth within the concrete. This is typically two inches from the bottom of a concrete slab.
6. Overlap is essential: When using rebar or wire mesh, pieces should overlap to create a continuous grid throughout the entire concrete piece.
7. Concrete cover: Ensuring that reinforcement materials are properly covered with concrete is critical to prevent rust and corrosion, which can compromise the structure.
By integrating these reinforcement strategies, your concrete will be better equipped to handle stress and load, and ultimately, stand the test of time.
Recap